Replacing Rudder Shelf
Moderators: CaptPatrick, mike ohlstein, Bruce
-
- Posts: 33
- Joined: Jun 29th, '06, 14:36
Replacing Rudder Shelf
I need to replace a rudder shelf because of rotting wood. Any problems with using 3/4" Starboard for the new shelf? Thanks.
Mike
Mike
- Skipper Dick
- Senior Member
- Posts: 330
- Joined: Jun 29th, '06, 08:22
- Location: Cape Coral, Florida
- Contact:
Rudder Shelf
Mike,
That's what I used, but I found that there are several densities of starboard. I used a piece of 3/4 starboard that was a little heavier than some other starboard I had. I think it works great.
Dick
That's what I used, but I found that there are several densities of starboard. I used a piece of 3/4 starboard that was a little heavier than some other starboard I had. I think it works great.
Dick
- CaptPatrick
- Founder/Admin
- Posts: 4161
- Joined: Jun 7th, '06, 14:25
- Location: 834 Scott Dr., LLANO, TX 78643 - 325.248.0809 bertram31@bertram31.com
Mike,
Starboard is a marginally workable material choice...
The first problem with Starboard, and other brands of polyethylene is it's very poor dimensional stability. The expansion and contraction ratio of the material is exceptionally high. The second item is you can not structurally bond anything to it. Mechanical fasteners only...
The third problem is that polyethylene is quite flexible and won't remain rigid when rudder forces are at play, especially at higher speeds.
In all reality, two pieces of 1/2" BC exterior plywood epoxy laminated together with a layer of 24 or 32 oz roving between will give you a very stiff 1 1/8" plank to work with.
After you cut to dimension, incapsulate it with 2 coats of epoxy. Figure out where the holes are going to be for the shafts and, using a hole saw, over size the holes so that you can fit flush sections of PVC pipe into the holes.
Then a full wrap of the rudder table(s) with 12 oz biaxle fabric, again using epoxy. Your final thickness will be about 1 1/4".
This will all take a bit longer than building with polyethylene, but you'll have a rudder table that's almost bullet proof and will stand up to the extreme forces when turning the boat at high speed.
Properly constructed and epoxy laminated plywood is a stong as you can get, (weight to strength ratio), and as long as you design to totally exclude water from ever getting to the wood, it'll last forever...
See the Boat Building Tips section for the various techniques involved with wood cores. http://bertram31.com/proj/tips/index.htm
http://bertram31.com/bailey/page3.htm will give you the basics of how I did the rudder shelf on Jim Bailey's boat. In this case I used expanded PVC Foam Board, but it was more expensive than plywood and can be a problem to find, depending on one's location...
Br,
Patrick
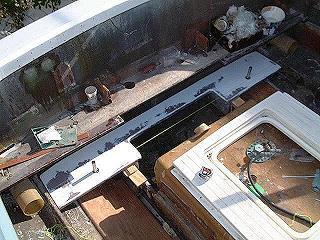
Starboard is a marginally workable material choice...
The first problem with Starboard, and other brands of polyethylene is it's very poor dimensional stability. The expansion and contraction ratio of the material is exceptionally high. The second item is you can not structurally bond anything to it. Mechanical fasteners only...
The third problem is that polyethylene is quite flexible and won't remain rigid when rudder forces are at play, especially at higher speeds.
In all reality, two pieces of 1/2" BC exterior plywood epoxy laminated together with a layer of 24 or 32 oz roving between will give you a very stiff 1 1/8" plank to work with.
After you cut to dimension, incapsulate it with 2 coats of epoxy. Figure out where the holes are going to be for the shafts and, using a hole saw, over size the holes so that you can fit flush sections of PVC pipe into the holes.
Then a full wrap of the rudder table(s) with 12 oz biaxle fabric, again using epoxy. Your final thickness will be about 1 1/4".
This will all take a bit longer than building with polyethylene, but you'll have a rudder table that's almost bullet proof and will stand up to the extreme forces when turning the boat at high speed.
Properly constructed and epoxy laminated plywood is a stong as you can get, (weight to strength ratio), and as long as you design to totally exclude water from ever getting to the wood, it'll last forever...
See the Boat Building Tips section for the various techniques involved with wood cores. http://bertram31.com/proj/tips/index.htm
http://bertram31.com/bailey/page3.htm will give you the basics of how I did the rudder shelf on Jim Bailey's boat. In this case I used expanded PVC Foam Board, but it was more expensive than plywood and can be a problem to find, depending on one's location...
Br,
Patrick
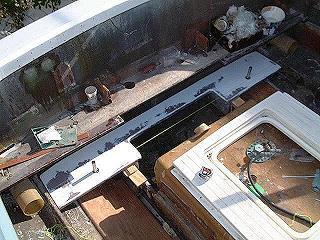
I replaced mine in my B35 per Capt Patrick's instructions it was a some what tedious process & I made it more complicated by cleaning and painting the whole area while I was in there. It's been over a year and half now and still looks good.
I also painted my steel steering tie bar with rustlock (don't recall the mfg, but it was from the Home Depot bought for another project). It stopped the continual rusting.
Good Luck.
Br,
JohnD
I also painted my steel steering tie bar with rustlock (don't recall the mfg, but it was from the Home Depot bought for another project). It stopped the continual rusting.
Good Luck.
Br,
JohnD
- Bulletproof
- Senior Member
- Posts: 43
- Joined: Jul 3rd, '06, 07:08
- Location: Marblehead, MA
- Contact:
I replaced my rudder shelf pretty much the way Patrick describes and made one mistake. When I slipped the rudder posts back up I somehow managed to get one side higher than the other. Now I can't get the shaft coupling on the starboard rudder post (above the bearing). I'm going to have to route down a pocket with my router now to get the bearing base down 1/2" so that it is at the right height to allow the shaft collar to sit where it belongs... Oh well. Don't worry Patrick, I'll seal the pocket before I mount the bearing base. And I'll drain weep holes incase any water builds up in the pocket.
Paul Haggett
B31 Bulletproof
Marblehead, MA
B31 Bulletproof
Marblehead, MA
Oh yeah, being a complete non-professional I did about 100 dry fittings at all different stages. Also, to anybody that really knows how to fiberglass my work kinda looks like my 4yr old did it. But from 6 ft away it looks clean and solid.
Look at it this way if the original marine ply unprotected lasted 25+ years a replacment with epoxy/glass should more than double that.
br,
JohnD
Look at it this way if the original marine ply unprotected lasted 25+ years a replacment with epoxy/glass should more than double that.
br,
JohnD
A bit of over kill on my part, but I used 1/2" fibreglass sheet (it was available) and also, while things were apart I removed the replaced the original wood support for the rudder-shaft housing with the same fibreglass sheeting. Pix possible if you want.
Mikey
Mikey
Mikey
3/18/1963 - -31-327 factory hardtop express, the only one left.
The difference between genius and stupidity is that genius has its limits.
-Albert Einstein
3/18/1963 - -31-327 factory hardtop express, the only one left.
The difference between genius and stupidity is that genius has its limits.
-Albert Einstein
-
- Posts: 33
- Joined: Jun 29th, '06, 14:36
Who is online
Users browsing this forum: Bing [Bot], Google [Bot] and 200 guests