We cranked it up and it ran just fine, all the hydraulics worked very well with no major leaks, oil was clear and even the brakes worked........so we bought it! ! !
When the South was hit with a hard freeze Chris and I was checking antifreeze in all of our "Stuff" and found that the backhoe had NONE......pure water! ! !.........it was late and we decided to simply drain it instead of going thru the antifreeze routing.
As Chris was removing the block drain he found the fly in the ointment........
Take a look
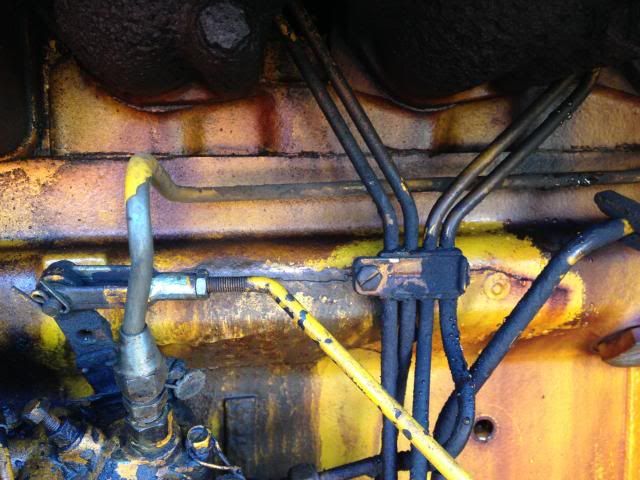
Yupp........cracked block in a water jacked just behind the injector pump
So....I read many years ago about a "Cast Iron" crack repair method that made pretty good sense to me..........What do I have to loose??
Getter all cleaned up and get started.
Notice the first 3 "Lock N Stitch" screws in the crack on the bottom of the water jacket.....
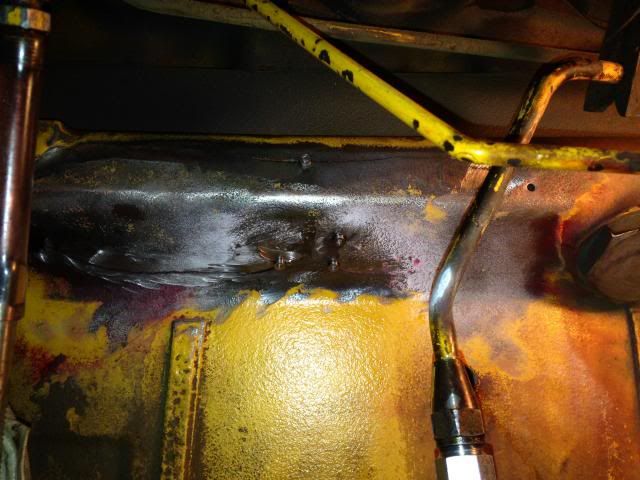
Now on to get started on the top of the crack.........drillin and tappin! ! ! !
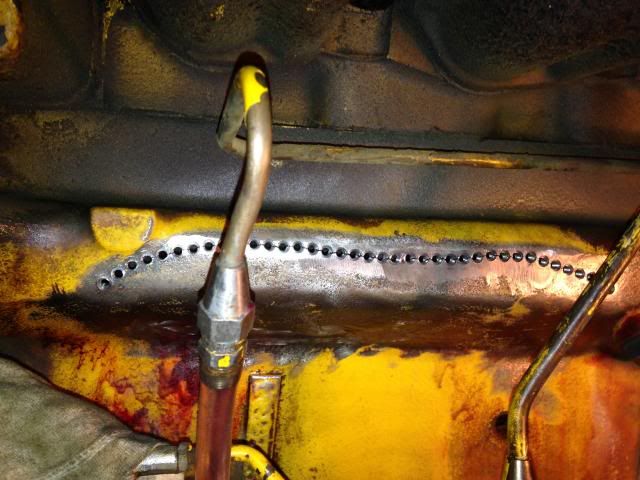
Drill and Tap with special tap.....install special threaded inserts then grind flush
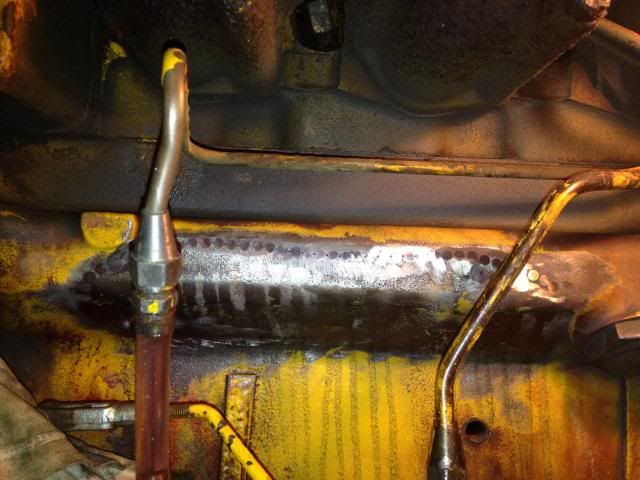
About 140 drilled and tapped holes later and walla...........success! ! ! ! !
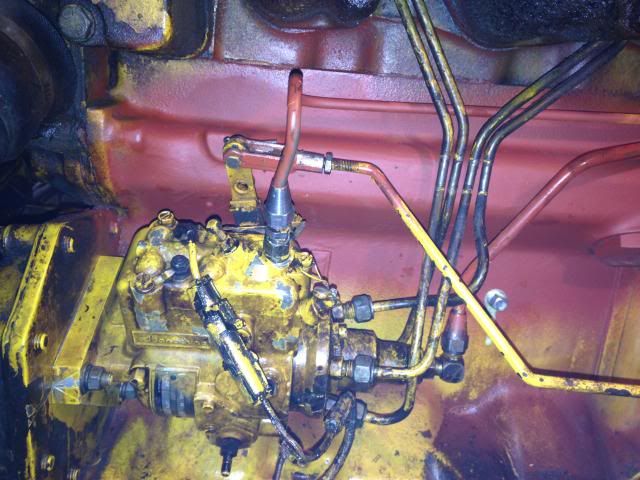
From here the proof will be in the PUDDIN...........we will see if the ole girl will pass the test of time
The name of the product that we used is Lock N Stitch .............we used the "C" Series screws
hb