Getting the core out wasn’t too bad. I did have to wack it pretty good with a block of wood. (you can see some evidence where I buggered up some of the tubes with the wood). I needed to hit it, not because it was frozen, but simply to move it. The fit is real tight. Nothing was corroded or frozen. I was surprised to see the inside of the air box is coated with some type of coating (epoxy?) and that coating was in great shape. I was scared from reading on the Tony Athens site about the bronze on aluminum corrosion issue, but the bronze doesn’t come in contact with the aluminum if the coating isn’t compromised. The fins of the core were pretty clean. I sprayed them with brake cleaner and there was not much to clean.
Going back together was pretty easy..I’m embarrassed to say that I installed the core in the wrong direction at first. There’s a little arrow showing the direction of the air flow. I had to take the core out again and reinstall. I greased everything with a marine grease with Teflon that I got at West marine. Tef gel might be better for the application but I couldn’t find it. Hope everything went back together right!!!
Did I miss anything guys?
Vince
Here’s some pics!
This is what I found when I took off the bottom cap.

Note the salt buildup???
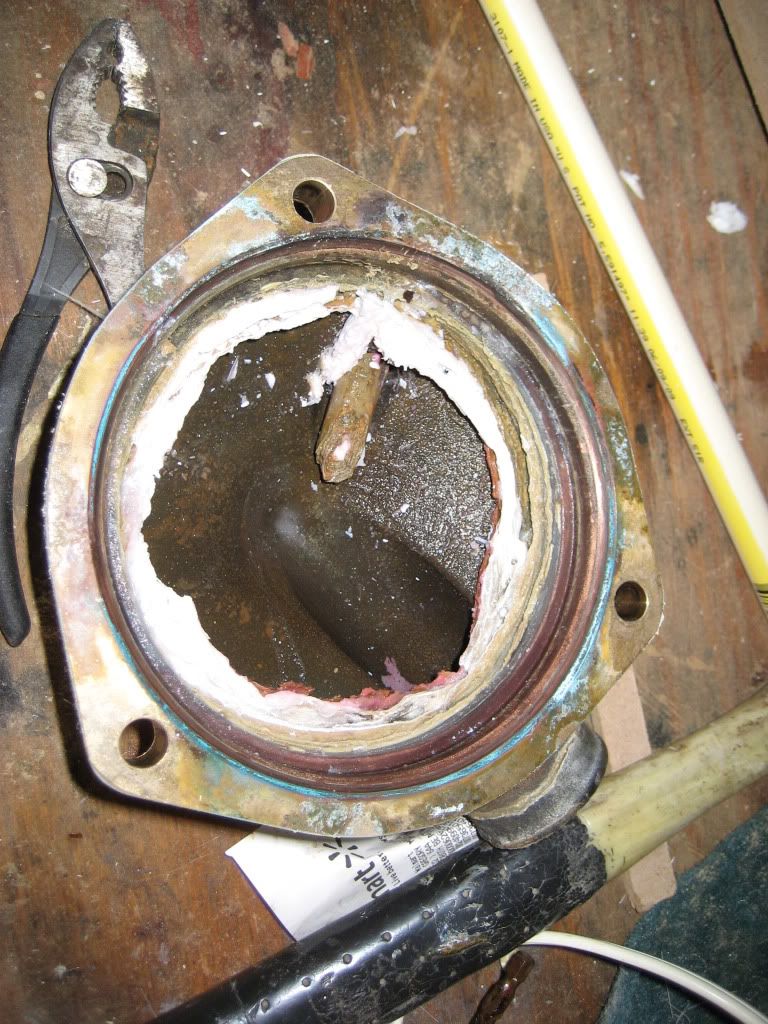
More of the same
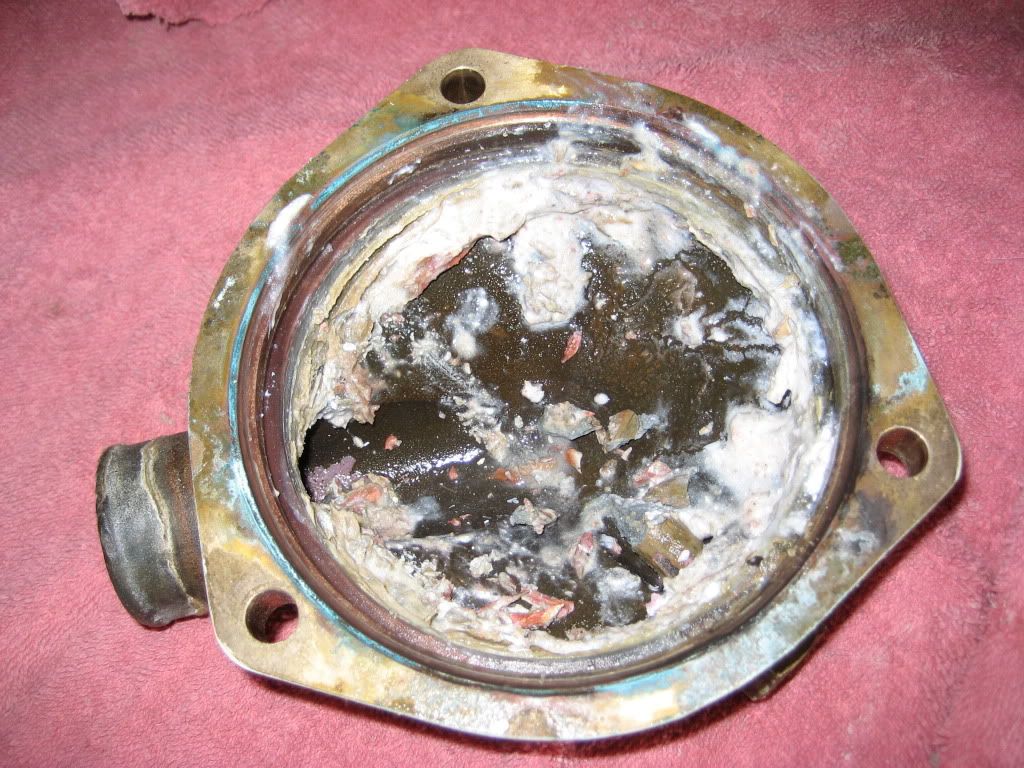
All cleaned up
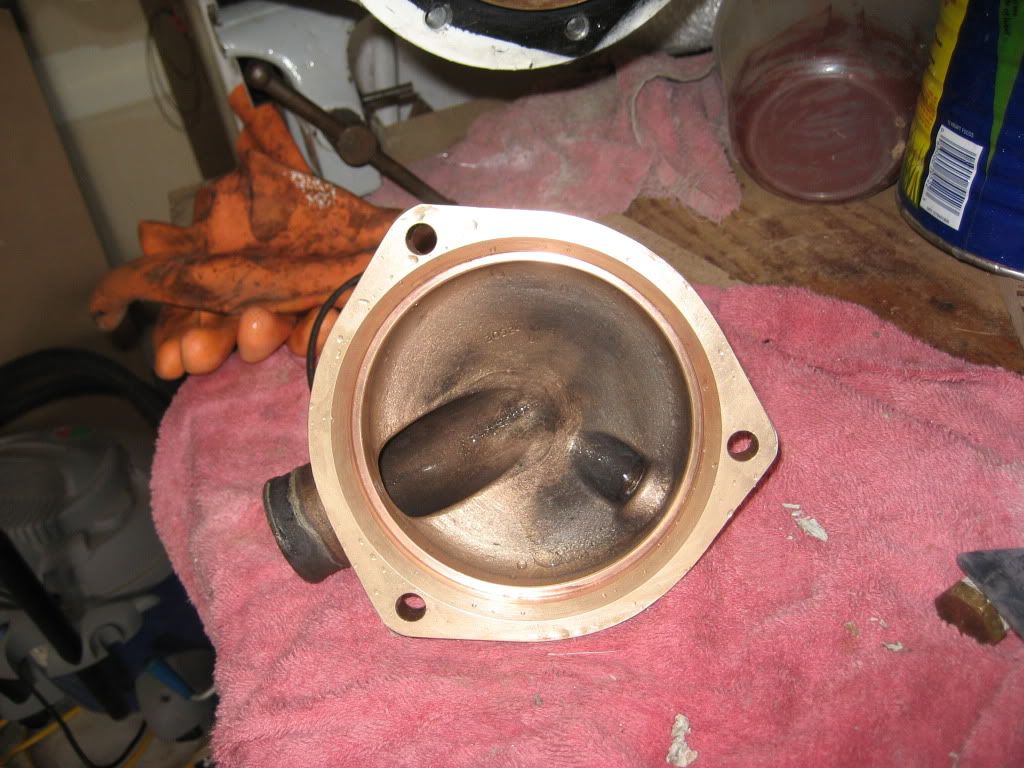
Top Cap. Note how much cleaner than the bottom.
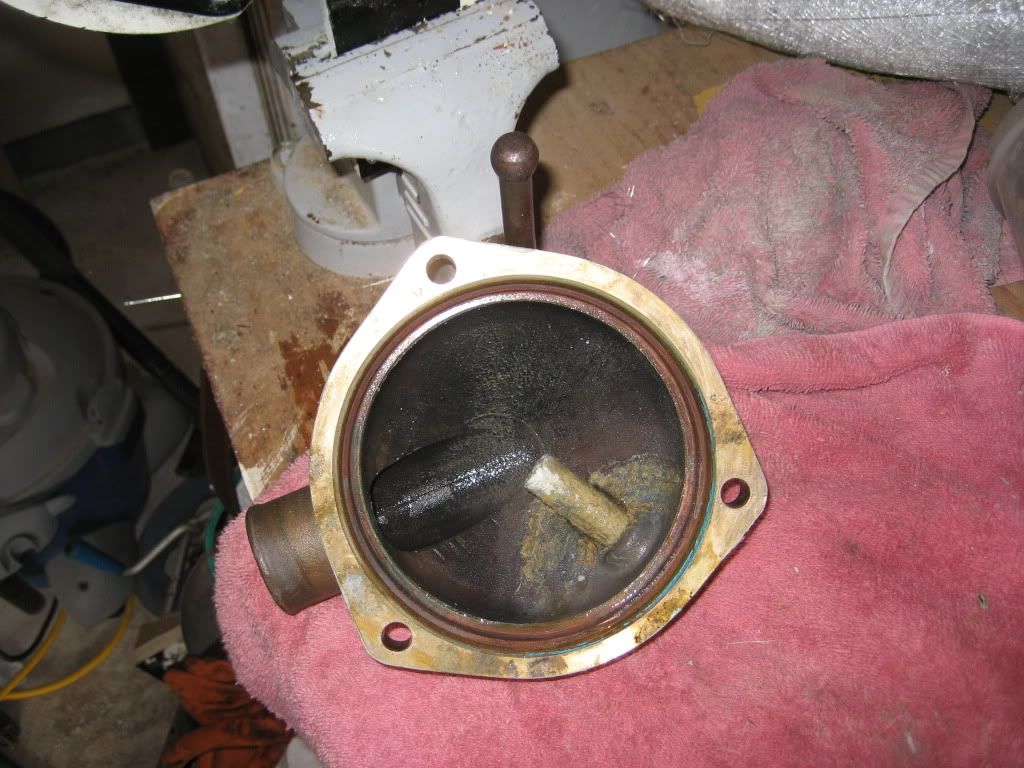
Here’s the core. Good shape!
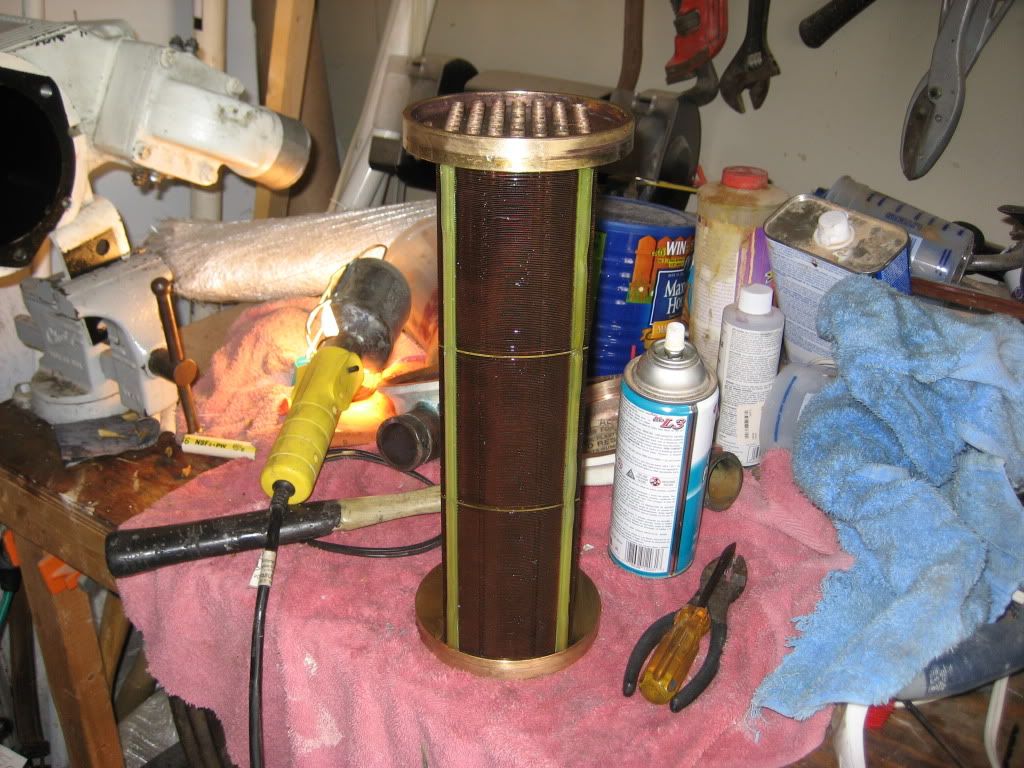
Air box looks real good and clean. Note the black coating.
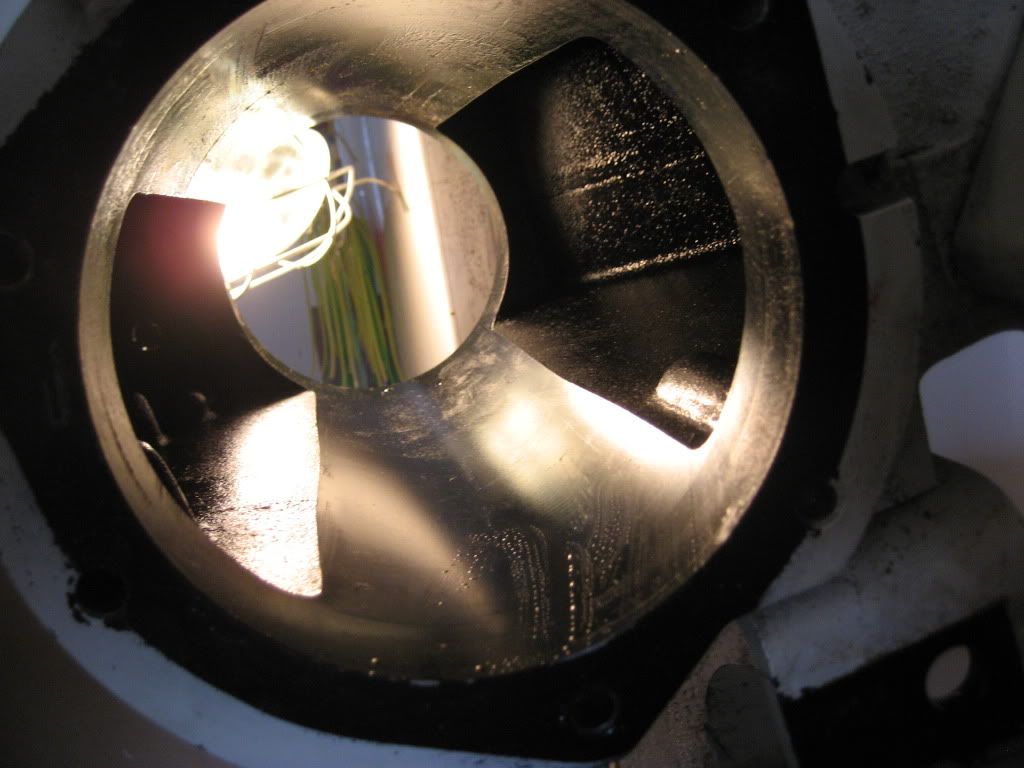
Core reinstalled, new O-ring and well-greased.
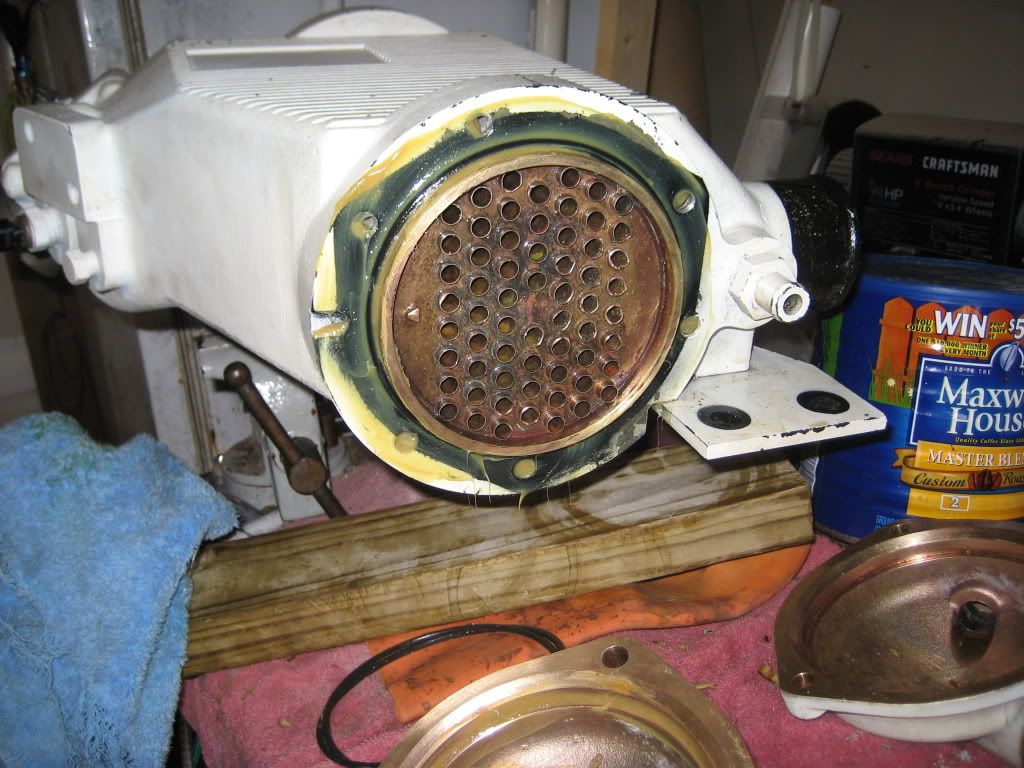
Back together.
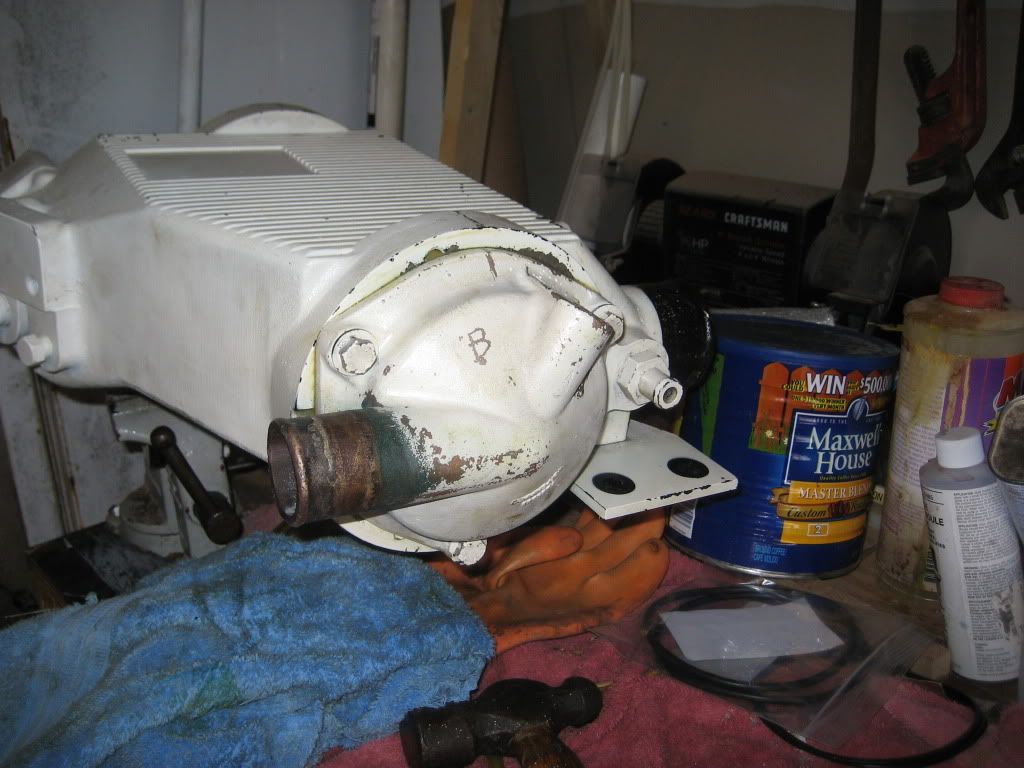