The Clorox chronicles, episode 9485.78
Moderators: CaptPatrick, mike ohlstein, Bruce
The Clorox chronicles, episode 9485.78
Todays chapter, Fun with Carver.
One of the repo boats I fixed, (frozen up turbo) got sold and I'm doing some work for the new owner who lives in Kalifornia and has the identicle 54 Carver out there also.
Why, I don't know. Its like having an ugly wife and girlfriend.
There is a glass moulded in swim platform 6'x12' to which the last owner added two jet ski skid rails and a hydraulic crane in the center to lift on and off.
To accomplish this they first covered the entire platform with 1/2" aluminum plate, one piece.
5200'd the entire thing down then thru bolted the entire platform, skid rails and crane based down thru the platform accesable thru the aft lazarette, barely.
Underneath they also use a 1/2" 5'x5' aluminum plate to support the cranes thru bolts.
The new owner wanted this all removed. All it takes is time and money right?
The crane, skid rails, crane base and under plate took a day and a half to undo.
The upper 1/2 aluminum plate remember is 5200'd down. To which I warned the owner by the time I got it up, good chance he'd be misiing some gel coat and glass.
Today I got a couple of cold chisels under the plate with much hammering. Took the 5200 debond and squirted around and after about 3 hours got about a foot on the side and about two feet on the back up enough to get the fork lift forks under since the cold chisels had a tendancy under the strees to pop back out.
I know this because one did just as I was climbing the ladder and hit me above the eye with a 2" gash and then the worst part was the chisel bounced off my head into the water and is gone.
With the yard workers staring in amazment at the amount of blood dripping I took my shirt off, held it over the cut, popped the first aid kit open in the truck, super glued it shut and bandaged the whole thing and went back to work.
Called the forklift over to put some up pressure to help the debond work. Everything was fine until I got close to the center where the 5" hole was cut thru the platform to below for the crane pole base and where the hydraulic lines came up thru.
The platform is balsa cored, was wet from the hole and with no strength started to rip a hugh chunk of the top layer of gel coat and what little glass they had supporting it. Nice, very nice.
Had the fork lift let the side of the plate down on a block under tension, sprayed the crap out of it with debond and will let the weekend do what ever its gonna do.
I'll take some pics on Monday as I'm sure there will be some big chunks of glass come off with that plate. Which just makes it harder to clean that plate off to keep..
One of the repo boats I fixed, (frozen up turbo) got sold and I'm doing some work for the new owner who lives in Kalifornia and has the identicle 54 Carver out there also.
Why, I don't know. Its like having an ugly wife and girlfriend.
There is a glass moulded in swim platform 6'x12' to which the last owner added two jet ski skid rails and a hydraulic crane in the center to lift on and off.
To accomplish this they first covered the entire platform with 1/2" aluminum plate, one piece.
5200'd the entire thing down then thru bolted the entire platform, skid rails and crane based down thru the platform accesable thru the aft lazarette, barely.
Underneath they also use a 1/2" 5'x5' aluminum plate to support the cranes thru bolts.
The new owner wanted this all removed. All it takes is time and money right?
The crane, skid rails, crane base and under plate took a day and a half to undo.
The upper 1/2 aluminum plate remember is 5200'd down. To which I warned the owner by the time I got it up, good chance he'd be misiing some gel coat and glass.
Today I got a couple of cold chisels under the plate with much hammering. Took the 5200 debond and squirted around and after about 3 hours got about a foot on the side and about two feet on the back up enough to get the fork lift forks under since the cold chisels had a tendancy under the strees to pop back out.
I know this because one did just as I was climbing the ladder and hit me above the eye with a 2" gash and then the worst part was the chisel bounced off my head into the water and is gone.
With the yard workers staring in amazment at the amount of blood dripping I took my shirt off, held it over the cut, popped the first aid kit open in the truck, super glued it shut and bandaged the whole thing and went back to work.
Called the forklift over to put some up pressure to help the debond work. Everything was fine until I got close to the center where the 5" hole was cut thru the platform to below for the crane pole base and where the hydraulic lines came up thru.
The platform is balsa cored, was wet from the hole and with no strength started to rip a hugh chunk of the top layer of gel coat and what little glass they had supporting it. Nice, very nice.
Had the fork lift let the side of the plate down on a block under tension, sprayed the crap out of it with debond and will let the weekend do what ever its gonna do.
I'll take some pics on Monday as I'm sure there will be some big chunks of glass come off with that plate. Which just makes it harder to clean that plate off to keep..
-
- Senior Member
- Posts: 340
- Joined: May 11th, '07, 16:13
- Location: Palm City, Fl.
- Contact:
I don't know if you are using the old original Debond or this new stuff I just saw someone praising on another forum. For the new stuff I doubt you will be able to get it for Monday, but it may be useful to clean up the aluminum plate.
Al
http://www.marineformula.com/index.htm
Al
http://www.marineformula.com/index.htm
NITES OFF
1978 B33 FBC
Al
1978 B33 FBC
Al
- Harry Babb
- Senior Member
- Posts: 2354
- Joined: Jun 30th, '06, 21:45
- Location: Fairhope Al
- Contact:
-
- Senior Member
- Posts: 340
- Joined: May 11th, '07, 16:13
- Location: Palm City, Fl.
- Contact:
- In Memory Walter K
- Senior Member
- Posts: 2912
- Joined: Jun 30th, '06, 21:25
- Location: East Hampton LI, NY
- Contact:
I give up Randall..what you got in there?
Surgury went well I hope.
Bruce...I got nothing. Jobs like that suck from beginning to end. Customer is pissy cause he wants it done and don't care. Sucks to do the job. Customer is now pissy because he "now does care".
Once in awhile you'll get one that will sing your praises for a job well done, but unfoutunetly they can be far and few in between.
Surgury went well I hope.
Bruce...I got nothing. Jobs like that suck from beginning to end. Customer is pissy cause he wants it done and don't care. Sucks to do the job. Customer is now pissy because he "now does care".
Once in awhile you'll get one that will sing your praises for a job well done, but unfoutunetly they can be far and few in between.
its a chunk of the radius that broke off and poked the skin. then there is another broken bone and lots of mangled tendons and ligaments. i walked around with it like that for a week because no dr would do the surgery with out a long list of other dr sign offs. i have an irregular EKG. the fact i play competitive volleyball with 30 year old ex national college champs and can surf double overhead storm surf didnt count.....i had to prove i was healthy enough for surgery while every hour of waiting made putting it back together harder and less precise.
sorry for the rant....pissed me off more then the accident.
sorry for the rant....pissed me off more then the accident.
- CaptPatrick
- Founder/Admin
- Posts: 4161
- Joined: Jun 7th, '06, 14:25
- Location: 834 Scott Dr., LLANO, TX 78643 - 325.248.0809 bertram31@bertram31.com
Had to remove a radar from my 31 on a gin pole, the pole was bolted & 5200 to the brow.. Im a mason for 42yrs so I used a "Rose" brick trowel.. very strong & thin .. beat it with a mash hammer .. you get the idea.. trowels are thin but tuff.
Wayne
Oh, says here in the book dont use a hammer on your trowel .. Never mind
Wayne
Oh, says here in the book dont use a hammer on your trowel .. Never mind
- CaptPatrick
- Founder/Admin
- Posts: 4161
- Joined: Jun 7th, '06, 14:25
- Location: 834 Scott Dr., LLANO, TX 78643 - 325.248.0809 bertram31@bertram31.com
5200 is not as strong as most people make it out to be.... The tricks to separating two parts bonded with urethane adhesive are knowing how to stress the material in order to break the bond and patience.
While most of the strengths of urethane adhesive are excellent, it's weakness lays in it's peel strength and inability to resist sustained peel pressure for more than a short duration.
To start, make up a bunch of hardwood wedges. The angle of the wedges should be between 15º and 20º. The wedge should be about 1 1/2" thick and about 2" wide, cut with the grain pattern of the wood running parallel to the length of the wedge. The larger the part to be removed, the more wedges you'll need. Pick the long edge of the part to be removed if possible.
Starting the process is the hardest step since initially you need to cut into the adhesive until the wedge penetrated deep enough to begin prying the two parts far enough away from one another to set up a constant stress on the adhesive. I often use wood chisels as my wedges to get the process started.
Once this has been achieved, progressively begin driving the wedges in deeper. Here's where the patience come in... Allow the wedges to remain until the adhesive along the stress line begin to fail. If you listen carefully, you can actually hear the adhesive failing after a very few minutes.
Generally, for 5200, allow about 5 minutes for the material to begin failing before driving the wedges in further. After every five minutes, drive the wedges deeper. Eventually the two parts will separate with minimal damage to either part, and even without the need for a de-bonding chemical. The more wedges you employ, the quicker the job will go, and with less damage to either part.
If the parts are so large that the initial wedges are getting lost between the parts, cut some more wedges but make them longer and/or thicker.
I've used this technique for years and on many parts bonded with 5200 and other urethane adhesives. When I've applied as much patience as I have force, it's never failed. The only problems encountered came from too few wedges & lack of patience...

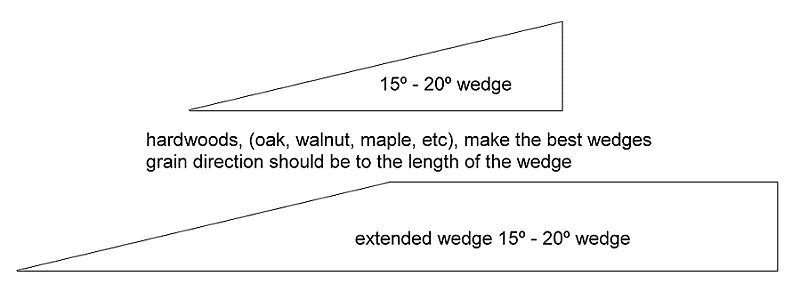
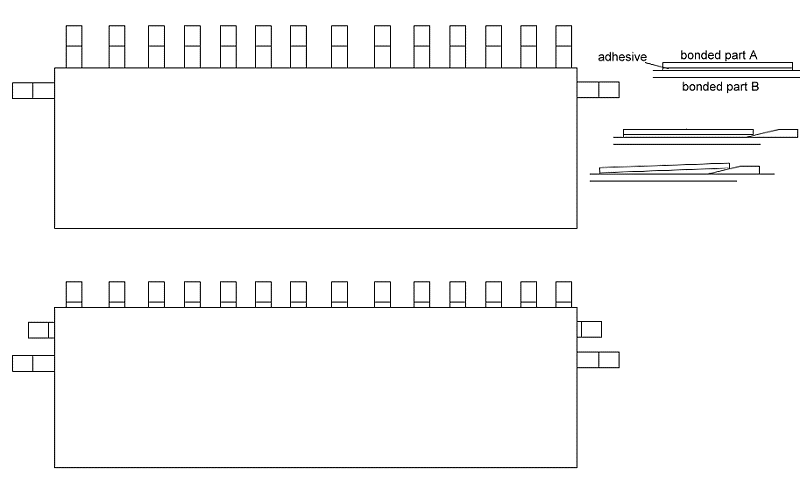
While most of the strengths of urethane adhesive are excellent, it's weakness lays in it's peel strength and inability to resist sustained peel pressure for more than a short duration.
To start, make up a bunch of hardwood wedges. The angle of the wedges should be between 15º and 20º. The wedge should be about 1 1/2" thick and about 2" wide, cut with the grain pattern of the wood running parallel to the length of the wedge. The larger the part to be removed, the more wedges you'll need. Pick the long edge of the part to be removed if possible.
Starting the process is the hardest step since initially you need to cut into the adhesive until the wedge penetrated deep enough to begin prying the two parts far enough away from one another to set up a constant stress on the adhesive. I often use wood chisels as my wedges to get the process started.
Once this has been achieved, progressively begin driving the wedges in deeper. Here's where the patience come in... Allow the wedges to remain until the adhesive along the stress line begin to fail. If you listen carefully, you can actually hear the adhesive failing after a very few minutes.
Generally, for 5200, allow about 5 minutes for the material to begin failing before driving the wedges in further. After every five minutes, drive the wedges deeper. Eventually the two parts will separate with minimal damage to either part, and even without the need for a de-bonding chemical. The more wedges you employ, the quicker the job will go, and with less damage to either part.
If the parts are so large that the initial wedges are getting lost between the parts, cut some more wedges but make them longer and/or thicker.
I've used this technique for years and on many parts bonded with 5200 and other urethane adhesives. When I've applied as much patience as I have force, it's never failed. The only problems encountered came from too few wedges & lack of patience...

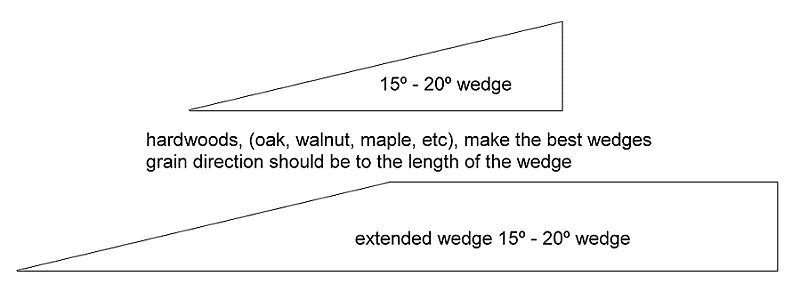
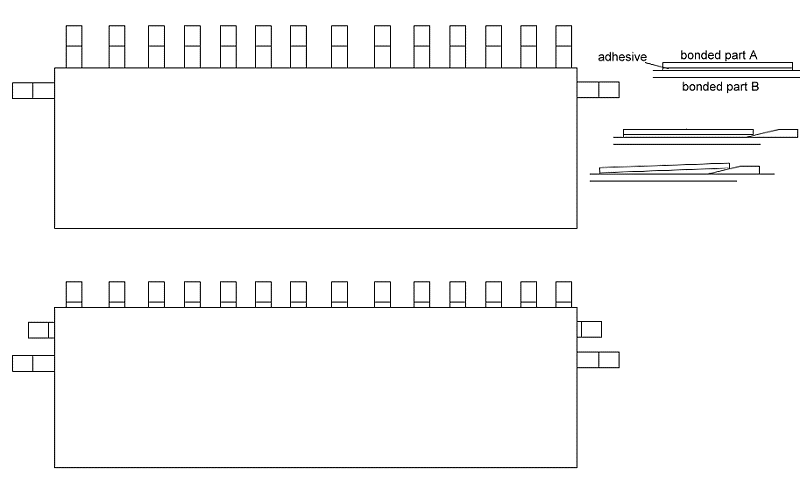
Walter,
I agree on the phone except being the middle man a good part of the time between the customer and a manufacturer or parts supplier I'd be on the phone all day going, ain't heard nothin yet.
Can't charge by the hour for that. And nobody wants to talk to anyone but me.
Pat, right you are on the wedges. thats how I got it to start to peel.
Tension, let it sit, spray debond listen to it peel then more tension.
Problem though is when the gel coat and or deck is weaker than the peel tension. Love balsa cored stuff that has holes drilled in it.
Oh BTW, got a Carolina Classic in Stuart I got to do some stuff to. Forgot how small that engine compartment was with those Cummins in there.
I agree on the phone except being the middle man a good part of the time between the customer and a manufacturer or parts supplier I'd be on the phone all day going, ain't heard nothin yet.
Can't charge by the hour for that. And nobody wants to talk to anyone but me.
Pat, right you are on the wedges. thats how I got it to start to peel.
Tension, let it sit, spray debond listen to it peel then more tension.
Problem though is when the gel coat and or deck is weaker than the peel tension. Love balsa cored stuff that has holes drilled in it.
Oh BTW, got a Carolina Classic in Stuart I got to do some stuff to. Forgot how small that engine compartment was with those Cummins in there.
- John Jackson
- Senior Member
- Posts: 161
- Joined: Jul 19th, '06, 22:39
- Location: Point Pleasant Beach, NJ
- CaptPatrick
- Founder/Admin
- Posts: 4161
- Joined: Jun 7th, '06, 14:25
- Location: 834 Scott Dr., LLANO, TX 78643 - 325.248.0809 bertram31@bertram31.com
Bob,
You're right about using heat, when possible. Most adhesives, including epoxies, begin breaking down at temperatures between 200ºF and 250ºF. For smaller metal parts, heating the part is a valid technique.
However, on large parts, the amount of heat required to bring the entire part up to 200º, and above, can become a daunting task. In the case of the 1/2" x 5' x 5' aluminum plate, no small torch or heat gun would ever deliver enough heat to do the job. Now a big welding rig set up to short across the plate might work.... Heating aluminum takes a ton of BTUs.
You're right about using heat, when possible. Most adhesives, including epoxies, begin breaking down at temperatures between 200ºF and 250ºF. For smaller metal parts, heating the part is a valid technique.
However, on large parts, the amount of heat required to bring the entire part up to 200º, and above, can become a daunting task. In the case of the 1/2" x 5' x 5' aluminum plate, no small torch or heat gun would ever deliver enough heat to do the job. Now a big welding rig set up to short across the plate might work.... Heating aluminum takes a ton of BTUs.
A rose bud on a cutting torch would do it I bet! I love mine! I work on my own heavy equipment and the best way to remove a large rusted on bolt is to heat it red hot and then quench it with water until you can put your hand on it. It will then usually come off fairly easily.
Back when I worked in a boatyard in highschool (30 years ago, ugh), one of my jobs was to remove and rebed the surface mounted plastic windows on those crappy Columbia sailboats. Some were 5200'ed on. I removed them using a set of 5 cheap stainless steel table knives. I would soak it in alcohol and slowly work the knives in one after the other to hold tension on it as it debonded. I would then leap frog the knives ahead to keep the tension on it. I wish they had debonder back then, the alcohol didn't do much but give me a headache!! The key was taking your time! I never broke one, but I did remove the occasional chunk of gelcoat!!
Not quite on the scale of Bruce's problem, but it agrees with Capt. Pat's more scientific observations!
Back when I worked in a boatyard in highschool (30 years ago, ugh), one of my jobs was to remove and rebed the surface mounted plastic windows on those crappy Columbia sailboats. Some were 5200'ed on. I removed them using a set of 5 cheap stainless steel table knives. I would soak it in alcohol and slowly work the knives in one after the other to hold tension on it as it debonded. I would then leap frog the knives ahead to keep the tension on it. I wish they had debonder back then, the alcohol didn't do much but give me a headache!! The key was taking your time! I never broke one, but I did remove the occasional chunk of gelcoat!!
Not quite on the scale of Bruce's problem, but it agrees with Capt. Pat's more scientific observations!
Rawleigh
1966 FBC 31
1966 FBC 31
When your dealing with a hugh heat sink like the 12' x 6' x 1/2" aluminum plate I removed, heat is really not an option.
It came off this am popped up about 4' when the tension released and fell on the ground. It took a 3' circle of gelcoat and coring with it.
All the glass fibers were dry where it ripped out indicating no strength due to the lack of resin penetration or just plain no resin.
Seems Bertram took its building techniques from Carver.
It came off this am popped up about 4' when the tension released and fell on the ground. It took a 3' circle of gelcoat and coring with it.
All the glass fibers were dry where it ripped out indicating no strength due to the lack of resin penetration or just plain no resin.
Seems Bertram took its building techniques from Carver.
ah 5200 - my buddies and I refer to it as "F" the next guy glue...
1977 B31 (315 Cummins) Build thread --->https://www.thehulltruth.com/boating-ho ... model.html
2010 Key West Bay Reef | 150 Yamaha
1986 Bertram 28 260 Mercruisers [SOLD]
2010 Key West Bay Reef | 150 Yamaha
1986 Bertram 28 260 Mercruisers [SOLD]
Who is online
Users browsing this forum: Google [Bot] and 122 guests