Page 1 of 1
Bathroom mold project
Posted: Feb 14th, '13, 23:18
by Joe E
This weeks project was the bathroom mold and part. Hope to get installed this weekend. I'll update other projects soon.
I used MDF to construct the mold off measurements taken off the boat. 1inch router bit was used to make a nice corner for the glass to lay on and a nice cosmetic look when the part is finished. inside edges were constructed using plastic filler(bondo) and a 1inch pipe.
Laying on a thinned coat of polyester primer to seal the MDF.
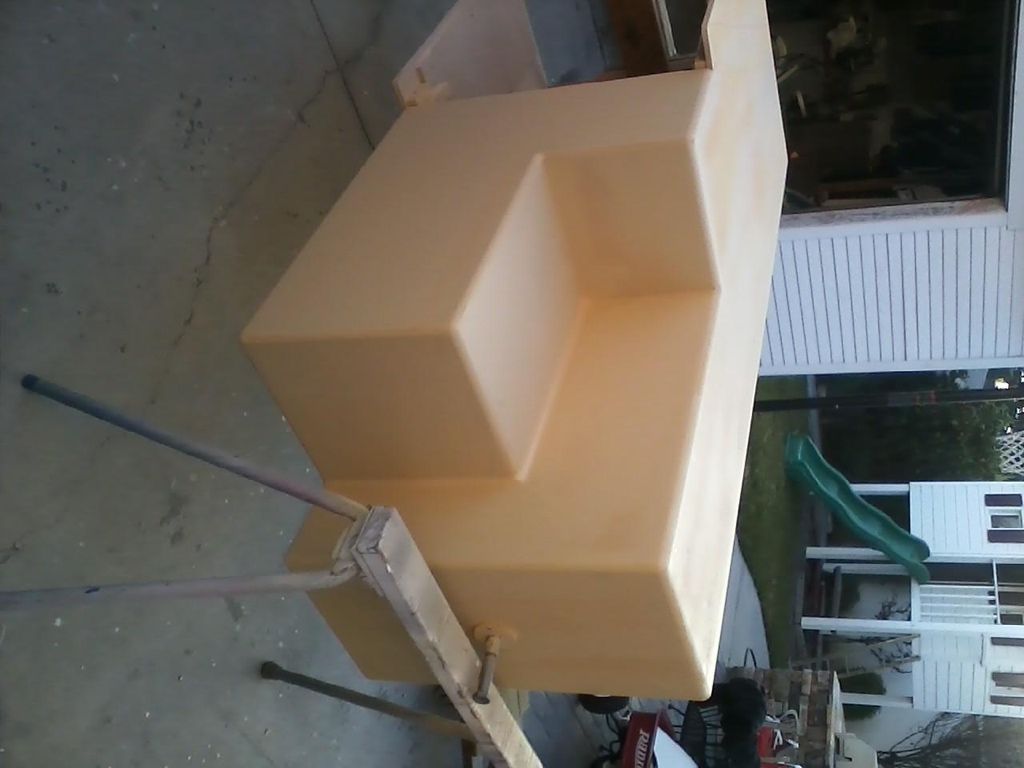
Block sanding
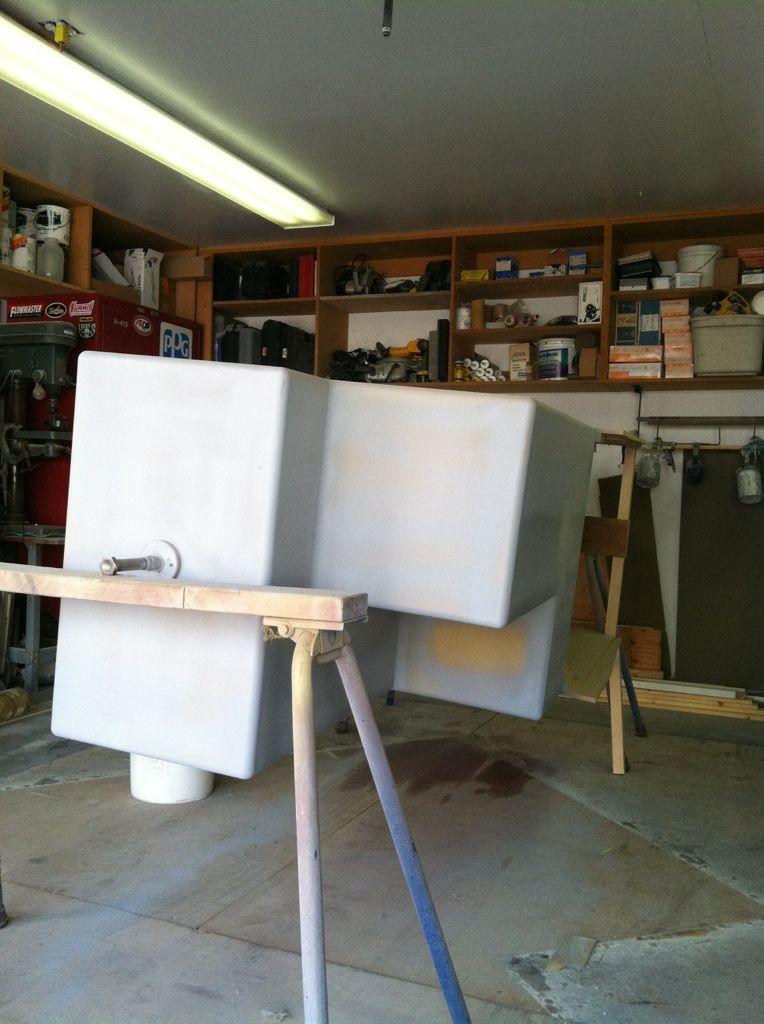
Waxing the mold. 5 coats
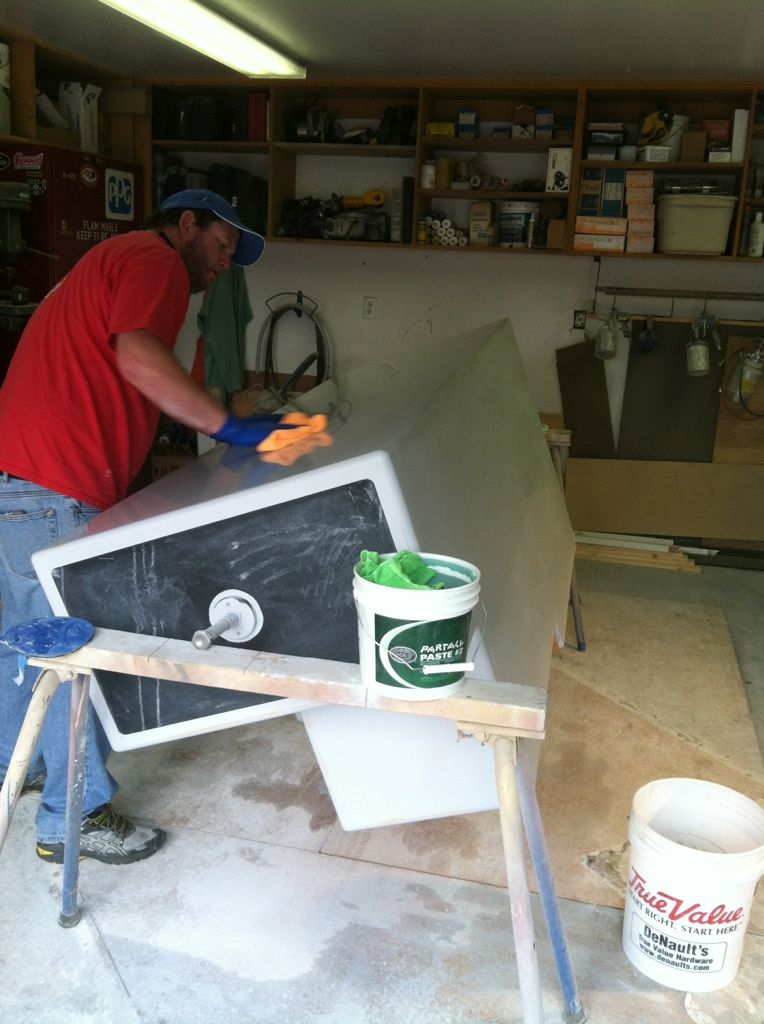
PVA sprayed and gel coat texture(black) for a non skid shower floor
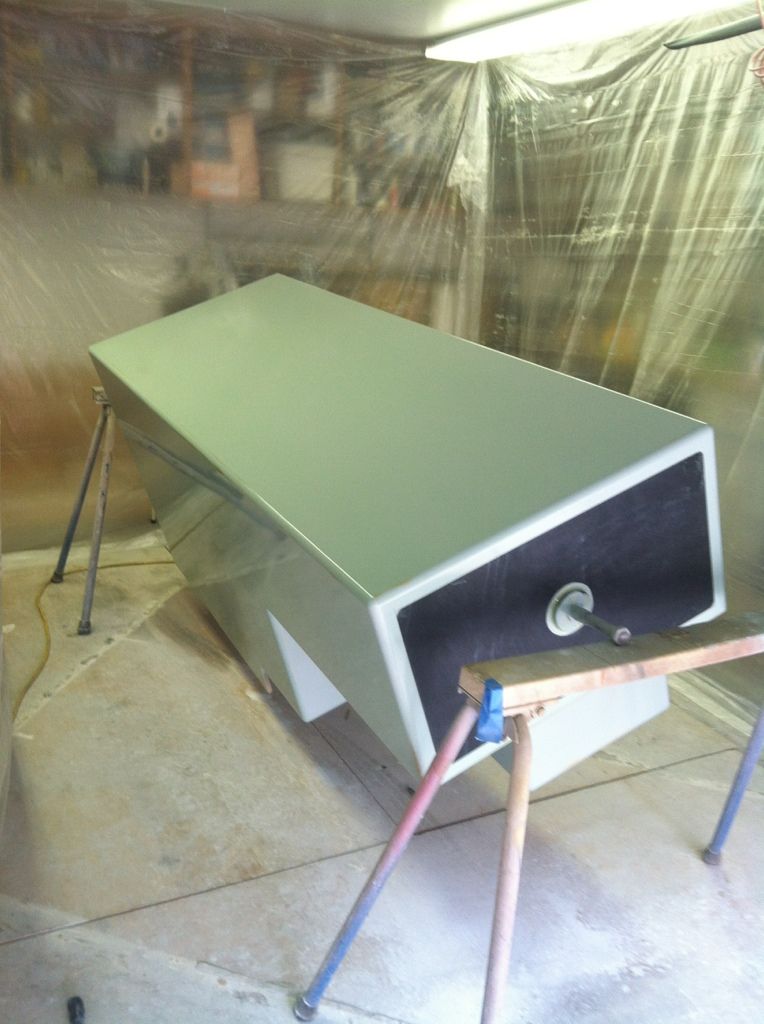
All the work in a big pile only way I could get the part out
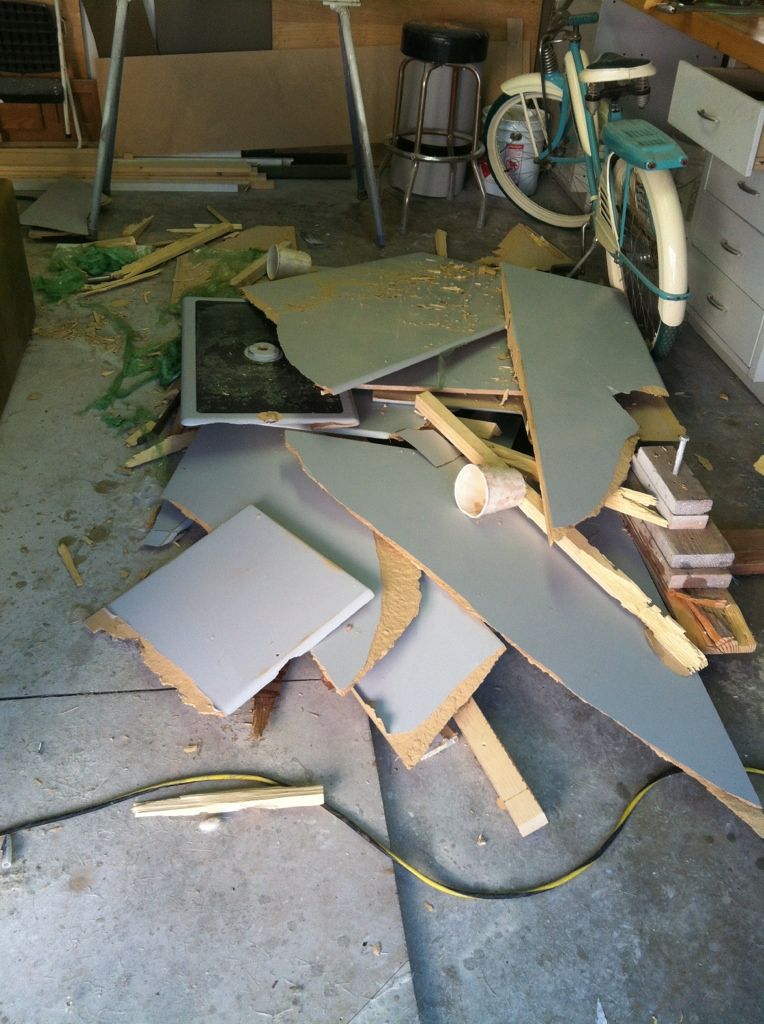
Finished part, gel coat and glassed, it's nice and glossy picture doesn't do justice
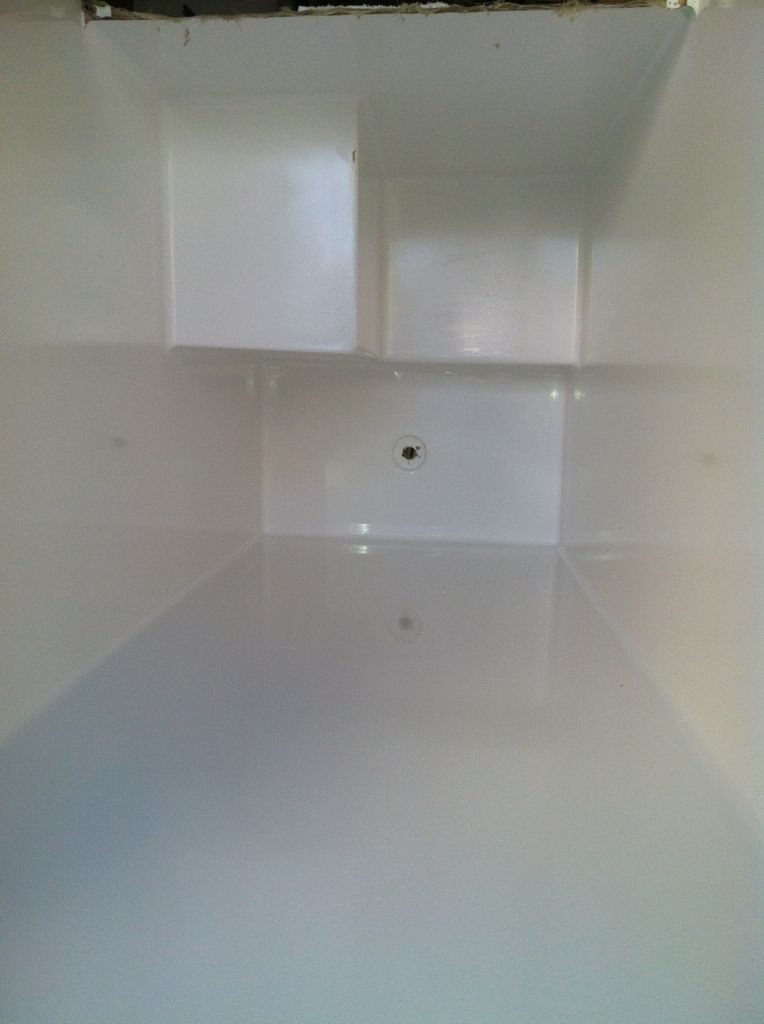
Re: Bathroom mold project
Posted: Feb 15th, '13, 09:50
by mike ohlstein
Nice. The big tub and shower manufacturers use a stainless steel mold that has pin-holes for water injection. They use water pressure to pop the piece from the mold.
Re: Bathroom mold project
Posted: Feb 15th, '13, 10:54
by CaptPatrick
Joe,
Well done on an ambitious project!
A few suggestions for future molding projects:
1. A new polyester mold needs to cure for at least 1 week before initial waxing/sealing to allow for complete out gassing of the styrene in the polyester. This will aid big time in how the part releases from the mold.
2. Rather than Partall PVA wax, seal the fully cured mold with a polymer sealant such as Meguires Machine Sealant, (2 applications is plenty...)
3. Use a
semi-permanent release agent over the sealant. This also requires a short, but necessary curing time.
4. Use a water based released agent over the above semi-permanent release agent. This will actually create the release happening between the two different release agents. (Here's a good source for a
variety of release agents.)
5. Create a positive draft in the mold design so that removal of part is possible.
6. include a 360ยบ flange at the base of mold for positive stopping point for the part. About 2" is sufficient and let your layup extend well onto the flange.
7. Include at least one compressed air fitting on the mold, (more may be required depending on part complexity), so that you can used a controlled compressed air release between the part and the mold. Use a valve to control the introduced pressure.
8. Allow the polyester part to cure for a minimum of 24 hours before attemting to remove from the mold.
9. Use a rubber mallet to apply moderate blows to the part and wedges around the flange as necessary to coax the part off of the mold while under air pressure.
I remember vividly my attempts to create a polyester molded part, either before learning these steps or by trying to cut corners and ignoring one or more of them. I too have left a few molds looking like your's in the final part removal...
Re: Bathroom mold project
Posted: Feb 15th, '13, 12:11
by Joe E
Thanks capt. Pat, your knowledge and info far exceeds anything I have seen or read else where. Ill use your advise on the next mold project. Do you still use the same process for your "one off" parts? I have many more molds to build but only for one part then I'm done with them. Thanks again Joe
Re: Bathroom mold project
Posted: Feb 15th, '13, 13:23
by CaptPatrick
Joe,
For a production mold I make it much heavier and better reinforced, but even one off molds need, and get, the same 9 step considerations... It's still easier to cut up and discard an intact one off mold than to tear the mold away from part. There's little difference in the mold building one way or the other.
Re: Bathroom mold project
Posted: Feb 15th, '13, 13:30
by Joe E
Thanks capt. Pat sent you an email. Joe
Re: Bathroom mold project
Posted: Feb 16th, '13, 08:25
by Craig G
That is beautiful. My bathroom mold project consisted of cleaning black mold off the vinyl wall covering in my Bahia Mar.