Page 1 of 1
Stainless question
Posted: Mar 3rd, '10, 11:42
by In Memory of Vicroy
Getting ready to order some fasteners in stainless & need advice from the Faithful. 18-8 stainless is 18% chrome, 8% nickel and is used in dinnerware (saw this on the History Channel). What is 316 and 304? One place I order from on the net sells 18-8 screws real cheap.....seems like they ought to last okay vs. the more expensive 316 and/or 304?
Inquiring minds need to know.....
UV
Posted: Mar 3rd, '10, 12:15
by Russ Pagels
Posted: Mar 3rd, '10, 12:19
by Carl
18-8 is an open term that has the 18-8 ratio you described. 304SS falls into that 18-8 range.
304SS is always 304SS and 18-8. But 18-8 is not always 304SS. I would use 304 above the waterline and would not use 18-8. There is more to the recipe then 3 ingredients.
316SS has higher strength and greater corrosion resistance then 304SS. One reason is due to the addition of molybdenum and more Nickel content.
Below the waterline 316SS is a must if your using SS, or you can go one better with 316L (has a lower carbon content).
Posted: Mar 3rd, '10, 15:51
by In Memory of Vicroy
Thanks, Faithful. As always, the authoritative source.
And to add yet another tidbit to the common pool of knowledge, Einstein's girlfriend he knocked up in Zurich was described as "unusually ugly".
UV
Posted: Mar 3rd, '10, 16:59
by CaptPatrick
Einstein's girlfriend he knocked up in Zurich was described as "unusually ugly".
Weren't any GQ Stud Model himself, but obviously knew how to tickle a girl's fancy...

Posted: Mar 3rd, '10, 19:43
by scot
316 if it is available in the parts, fasteners, etc that you needs. 304 will bleed.
Posted: Mar 3rd, '10, 22:17
by gplume
This should settle the story on which steel to use....316 looks to be the most noble in all situations. There is abig differnce between passivated and active versions.
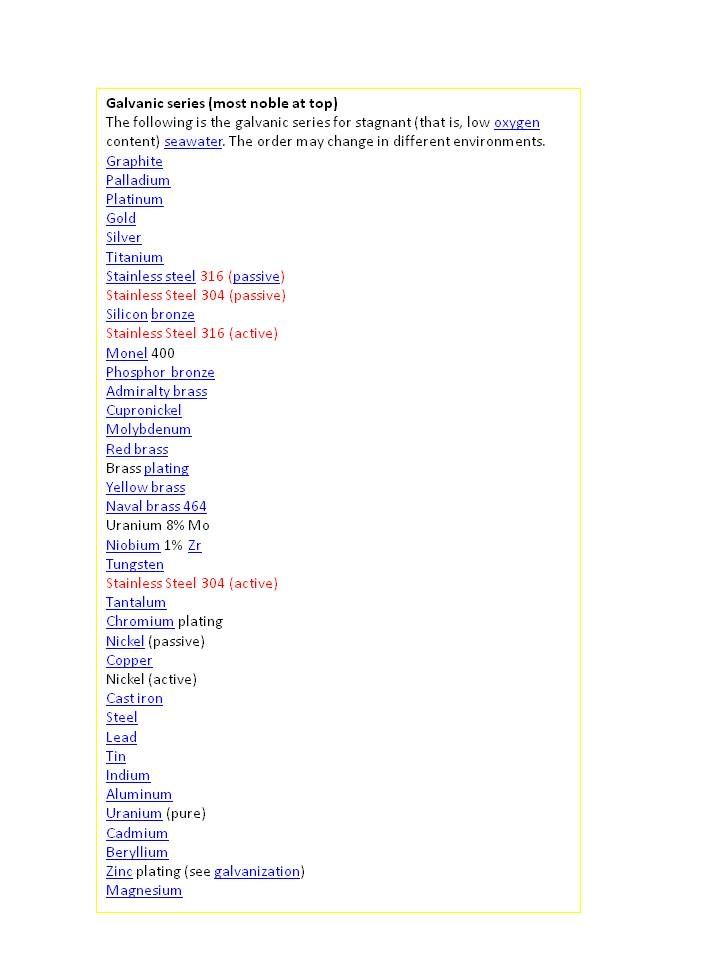
Posted: Mar 4th, '10, 08:21
by tunawish
Vic,
Just make sure the hardware is not being produced in China. I've found out the hard way recently from 2 suppliers I've used for 15+ years. When I called them with bleeding complaints they admitted they had started outsourcing overseas.
The 316L from China is not always the same as 316L from here....
Ray
Posted: Mar 4th, '10, 10:23
by In Memory Walter K
I'm not surprised.
Posted: Mar 4th, '10, 11:11
by mike ohlstein
'Bleeding' can sometimes be caused by using non-stainless tools during the installation of stainless hardware. Stainless steel loves free iron. Iron rusts.
Posted: Mar 4th, '10, 11:39
by AndreF
Good point, Mike, I have a SS 1/2 tower (it's a real pain in the a$$) and my welder told me to always clean it w/a SS brush after working on it w/anything.
Posted: Mar 4th, '10, 11:43
by tunawish
Mike,
Your right about the tools and that's the first thing they said when I called them,
But I had them look up the invoice.. I had ordered 6 sets of SS philips tips from them with the order..
They sent replacement screws but I've lost confidence in the product and never put them back on the boat..
Posted: Mar 5th, '10, 08:48
by Carl
AndreF wrote:Good point, Mike, I have a SS 1/2 tower (it's a real pain in the a$$) and my welder told me to always clean it w/a SS brush after working on it w/anything.
You have to watch with the SS brushs too! Ordered a replacement SS wire wheel that we use to Spiff up welds before shipping. My customer calls me up yelling that I did not use SS as the parts are rusting. I knew I used the correct materials, and I didn't overheat the materials when welding another way to loose corrosion resistance, but jumped in the truck and ran over to his place to see what he was talking about...sure enough the area around each weld where the Wire Wheel touched showed signs of rust. Anyway, I ran back to the shop grabbed my Pickling paste and let it do it's thing and all was good again. Long story short the Wire Wheel was SS at least it was marked that way...but when I called up my Welding supply house they already knew about it and shipped me a replacement...seems they got a "Good Deal" on SS wire wheels.
Posted: Mar 6th, '10, 00:51
by In Memory Walter K
Made in China?
Posted: Mar 6th, '10, 08:55
by Carl
This was years ago when China only made Cheaply made Knockoffs you would even consider using.
China...it was a big problem for us with their cheaply made knockoffs. I think we are starting to encounter a new bigger problem...they are now producing some good quality products. I try to avoid Cheap imports, but every now and then one sneaks in and I wonder how they can make something so inexpensively...case and point,
"Chick" a USA made double vise cost $1100.00. I have one, but needed 3 more for a job. I found an import in a sales flyer at $199.00. Figured it was crap..but thought maybe I could make it work so bought one to take a look at it. The import needed some "tweaking" here and there to get it to work for me, but all the working surfaces where on the money...hate to say it but I purchased 3 imports for that job. If I incorporated the additional tooling cost into the job, I would have lost the job...you know where the job was going to go if we lost it...yep to China.
Oops, did the tangent thing again...UV, buy USA 316SS hardware.
Carl
Posted: Mar 7th, '10, 00:38
by Peter
Off point, but interesting:
STAINLESS was borne from " it stains less" as opposed to "stain free"
No one ever said it couldn't rust. Just that it rusted less.
Various grades deal with hardness, magnetic properties, stain resistence etc... but mostly the XXX grading is BS. Just for marketing: like selling "facial tissue" as "Kleenex." No two suppliers are exactly alike.
Peter
Posted: Mar 7th, '10, 07:35
by randall
mike ohlstein wrote:'Bleeding' can sometimes be caused by using non-stainless tools during the installation of stainless hardware. Stainless steel loves free iron. Iron rusts.
this is why the shoreham nuclear plant never opened. too many bad SS welds to fix.
Posted: Mar 7th, '10, 09:32
by Carl
Peter wrote:Off point, but interesting:
STAINLESS was borne from " it stains less" as opposed to "stain free"
No one ever said it couldn't rust. Just that it rusted less.
Various grades deal with hardness, magnetic properties, stain resistence etc... but mostly the XXX grading is BS. Just for marketing: like selling "facial tissue" as "Kleenex." No two suppliers are exactly alike.
Peter
I'll agree with everything with exception to the XXX grading is BS.
While it is true each Steel Mill has there own recipe for a material grade, they must conform to the basic Grade recipe. Sometimes the differences can be subtle between companies and other times you will find huge differences. Some companies produce a very consistent product while others you will see the product vary a good deal.
304SS and 303SS both 18-8 and for the most part exactly the same ingredients and properties. One exception in 303 they add less then 1% sulfur to the mix. That minuscule amount of sulfur will enable machining time to be reduced by at least 1/3 and extend the life of the tooling several times over. Down side of 303SS, it does not weld very good, it does not machine to the same luster as 304 and some products cannot have that idy bit of Sulfur content.
Now take that 303SS and purchase from different mills, all with the same 303 Certification and you will see different properties. Kind of like going to different restaurants and ordering the same dish. Each may have a good and bad point. Then comes consistency...if you go back to that same place with friends and family...will it be the same or is it hit and miss?
Now look at 400 series SS...it is magnetic and will rust over almost as quickly as steel...but it can be hardened and for all intensive purposes it will Stain-less or rust-less then Steel.
Posted: Mar 7th, '10, 09:38
by bob lico
hold on randall the steam fitters local 638 had the best welders in the world on instumentation (stainless piping usually 1/2" or less in diameter).they start life at 6 years old with a stick in there hand , sort of like a tradition handed down from father to son from the island of trinadad and tabarco . back then in 1978 they were paid 2 grand a week .the powerhouse reactor will flood as a last step to cool from 8 -12" everdor pipes coming thru a screen well from long island sound those guys were the only one who could well it. the stainless problem was in the screenwell because the anodes to protect were killing little fish that were attacted to the warm outflow.local population and treehuggers saw the fish floating they pull out the anodes and had to deal with stainless selfdestructing in saltwater.basicly we killed the safest nuclear powerhouse ever built and 5 billion dollars total that 3 generation of long islanders will paid . they got it on the technicallity that the emergency generators (6) one to back up each other one would not start and produce power (1200hp engines) in 50 seconds! that was the requirement by feds.lastly long island has only one way out for evacuation and you know this could never be done from day one.that powerhouse would have really helped long island with the largest oil fired plant in the world and the furthest from the source.i worked with engineering startup for 5 years and learn what politics could do!!!
Posted: Mar 7th, '10, 09:47
by Charlie J
shoreham didnt open because there was to much stainless walking off the job lol. i understand they were losing $100,000 per month on materil that was stolen, and someone told me yars ago the expected that # and it was coverd in the bid.
Posted: Mar 7th, '10, 10:04
by tunawish
Sim
"Idy Bit".....??? What engineering book did that come from ??...
Obviously you know what your talking about but to see that thrown in there, cracked me up....
Ray
Posted: Mar 7th, '10, 10:09
by bob lico
charlie honestly i seen stainless 24' boat trailers being made in one of the pre-fab shops. to this day nobody can tell me differant about welding .you have to belive passing the nuclear welding test has to be the hardest i have ever seen in my whole life in any person`s respective trade.from those days on i remember the best alluminum welder i had ever seen or heard of bernie shackner welded with gas and stood up to the most riggerous testing you ever seen. basiclly it takes 4 days for two men to weld one joint on critical welds (piping). preheating took two days alone and a tent was built over every weld.
Posted: Mar 7th, '10, 11:40
by Carl
Yes "Idy Bit", that just a skosh more then a "Teeny Weenie Bit".
Says it right here in my "Super-Duper Machinist Handbook for Dummies".