Exhaust Outlet?
Moderators: CaptPatrick, mike ohlstein, Bruce
- scot
- Senior Member
- Posts: 1470
- Joined: Oct 3rd, '06, 09:47
- Location: Hurricane Alley, Texas
- Contact:
Exhaust Outlet?
I know that polyester should be used to fabricate the surge fitting due to temp, but can epoxy be used at the stern as the primary bond on a fiberglass thru-hull?
Thanks
Thanks
Scot
1969 Bertram 25 "Roly Poly"
she'll float one of these days.. no really it will :-0
1969 Bertram 25 "Roly Poly"
she'll float one of these days.. no really it will :-0
I don't see why you couldn't.
The one advantage the polyester had for us was that if "kicked" faster than the epoxy. After holding the tube in place with a few claw glass fillets I cut small pieces of chop and started moving around the tube. Then took a strand or 3 of heavy roving and put that around and over the chop. I worked this until I felt there was enough meat to support any loading the piece might get during the tubing installation. I did this to both sides of each tube.
When I tried a similar technique with the expoxy I found that it would run out of the fiberglass leaving it dry on top and saturated on the bottom before it "kicked" You may have an advantage in the Texas sun and not have to worry at all, but that was the issue I had.
Is there a reason you need epoxy? or is just cause you got some left? Big tube little tube?
The one advantage the polyester had for us was that if "kicked" faster than the epoxy. After holding the tube in place with a few claw glass fillets I cut small pieces of chop and started moving around the tube. Then took a strand or 3 of heavy roving and put that around and over the chop. I worked this until I felt there was enough meat to support any loading the piece might get during the tubing installation. I did this to both sides of each tube.
When I tried a similar technique with the expoxy I found that it would run out of the fiberglass leaving it dry on top and saturated on the bottom before it "kicked" You may have an advantage in the Texas sun and not have to worry at all, but that was the issue I had.
Is there a reason you need epoxy? or is just cause you got some left? Big tube little tube?
KR
JP
1977 RLDT "CHIMERA"
JP
1977 RLDT "CHIMERA"
- scot
- Senior Member
- Posts: 1470
- Joined: Oct 3rd, '06, 09:47
- Location: Hurricane Alley, Texas
- Contact:
Thanks JP,
I believe I read (on this site) once that epoxy should not be used in the exhaust system because it starts melting at 250 degrees.
Epoxy is all I use on repair/rebuild work. Most of the transom on my boat has been rebuilt / modified with the 1/2 pocket and all of the work is in epoxy. I have always heard that you "can put epoxy onto polyester...but you can't put polyester on epoxy"
So, if I cannot use the epoxy to bond in the exhuast fitting, I will be forced to use a bronze thru-hull.
I buy it in the 5 gal pals and basically use it for everything. I would mix an epoxy+milled fiber+ cabosil putty to install the pipe, "if" epoxy is OK here. I would completely pack the gap and use a generous fillet on the inside and outside.
I believe I read (on this site) once that epoxy should not be used in the exhaust system because it starts melting at 250 degrees.
Epoxy is all I use on repair/rebuild work. Most of the transom on my boat has been rebuilt / modified with the 1/2 pocket and all of the work is in epoxy. I have always heard that you "can put epoxy onto polyester...but you can't put polyester on epoxy"
So, if I cannot use the epoxy to bond in the exhuast fitting, I will be forced to use a bronze thru-hull.
I buy it in the 5 gal pals and basically use it for everything. I would mix an epoxy+milled fiber+ cabosil putty to install the pipe, "if" epoxy is OK here. I would completely pack the gap and use a generous fillet on the inside and outside.
Scot
1969 Bertram 25 "Roly Poly"
she'll float one of these days.. no really it will :-0
1969 Bertram 25 "Roly Poly"
she'll float one of these days.. no really it will :-0
- CaptPatrick
- Founder/Admin
- Posts: 4161
- Joined: Jun 7th, '06, 14:25
- Location: 834 Scott Dr., LLANO, TX 78643 - 325.248.0809 bertram31@bertram31.com
Scot,
Here's how I do it...
Cut the hole for the exhaust tube and scarf the exterior at 12:1. Fit the pipe to be a snug fit in the hole.
Build a flange onto the pipe with Coosa Board, or similar product, and corresponding to the transom angle. With the pipe in place, tack the flange to the pipe. Thickened polyester is fine. Remove the assembly and glass the flange to the pipe with polyester and chopped strand mat.
Now, install the finished flanged pipe and bed with thickened epoxy. No additional glass work reqiuired...
Rebuild the exterior joint with polyester and glass, epoxy fair, and you're ready for paint.
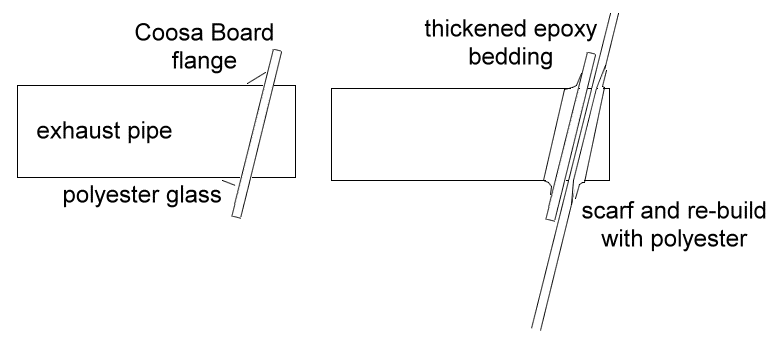
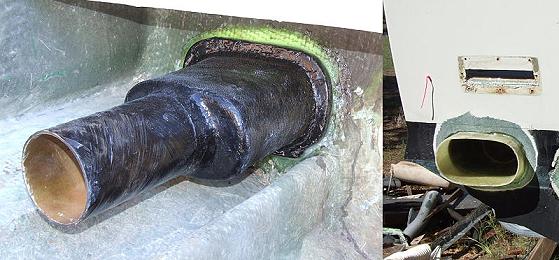
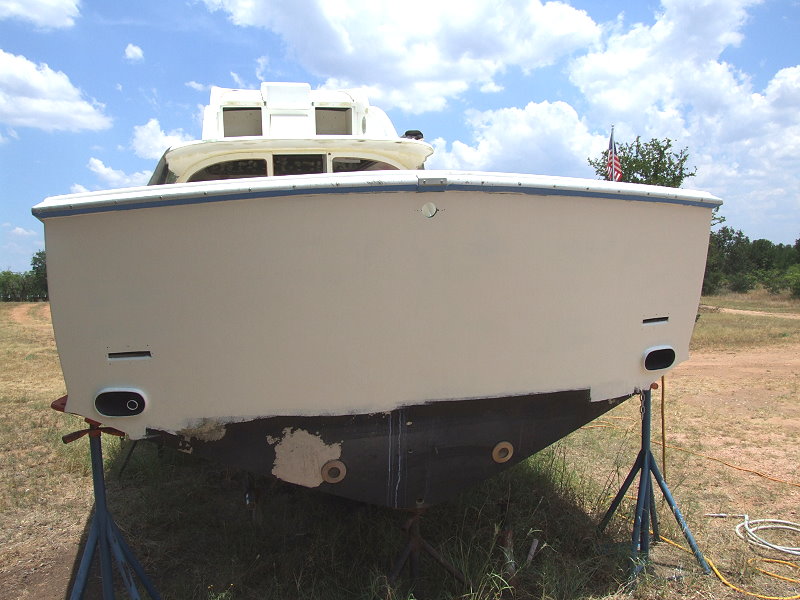
Here's how I do it...
Cut the hole for the exhaust tube and scarf the exterior at 12:1. Fit the pipe to be a snug fit in the hole.
Build a flange onto the pipe with Coosa Board, or similar product, and corresponding to the transom angle. With the pipe in place, tack the flange to the pipe. Thickened polyester is fine. Remove the assembly and glass the flange to the pipe with polyester and chopped strand mat.
Now, install the finished flanged pipe and bed with thickened epoxy. No additional glass work reqiuired...
Rebuild the exterior joint with polyester and glass, epoxy fair, and you're ready for paint.
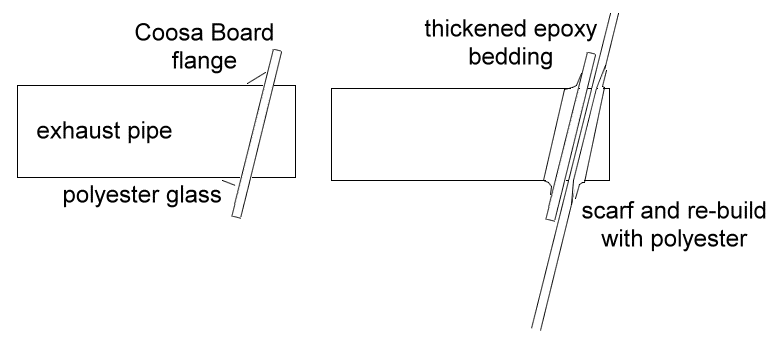
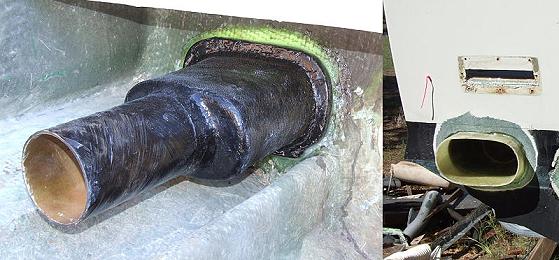
- scot
- Senior Member
- Posts: 1470
- Joined: Oct 3rd, '06, 09:47
- Location: Hurricane Alley, Texas
- Contact:
Capt Patrick,
My B25 transom is already epoxy, I had to fill (2) I/O holes and have built a shallow pocket, cored and cloth inside, all epoxy. So, what ever I do it will be tying into an epoxy base material.
Based on your comment;
Also, I see the need for the flange plate on a bare glass transom (it's thin), but I don't think I would need the plate on a 2" thick cored transom would I? ...it's only cored in the 25's "bubble" area, but that's where the fitting will be located.
The image shows the design of the installation;
The thru-hull is going throught the cored area.
Thanks
My B25 transom is already epoxy, I had to fill (2) I/O holes and have built a shallow pocket, cored and cloth inside, all epoxy. So, what ever I do it will be tying into an epoxy base material.
Based on your comment;
It is OK to bed and secure the fitting with epoxy, why would you scarf and rebuild with polyester outboard rather than finishing with epoxy?Now, install the finished flanged pipe and bed with thickened epoxy
Also, I see the need for the flange plate on a bare glass transom (it's thin), but I don't think I would need the plate on a 2" thick cored transom would I? ...it's only cored in the 25's "bubble" area, but that's where the fitting will be located.
The image shows the design of the installation;

The thru-hull is going throught the cored area.
Thanks
Scot
1969 Bertram 25 "Roly Poly"
she'll float one of these days.. no really it will :-0
1969 Bertram 25 "Roly Poly"
she'll float one of these days.. no really it will :-0
- CaptPatrick
- Founder/Admin
- Posts: 4161
- Joined: Jun 7th, '06, 14:25
- Location: 834 Scott Dr., LLANO, TX 78643 - 325.248.0809 bertram31@bertram31.com
Scot,
I do the flange just to exclude the need to get down and glass in the tight area. Remember, this is a B31, out board, under the deck ledger, and real close to the hull underneith and outboard.
You may have more working room in your rig... If your exit hole is solid epoxy, then stick with epoxy. Use a medium fast setting epoxy, mixed primarily with cabosil, and do the job early in the morning when the temperature is still in the 70's. It'll be set before the hot afternoon temps get there. Once the construction joint has been made you can go to a less thixothropic mix for fairing. I'd still do some undercutting and go for a fileted joint between the pipe and transom.
I do the flange just to exclude the need to get down and glass in the tight area. Remember, this is a B31, out board, under the deck ledger, and real close to the hull underneith and outboard.
You may have more working room in your rig... If your exit hole is solid epoxy, then stick with epoxy. Use a medium fast setting epoxy, mixed primarily with cabosil, and do the job early in the morning when the temperature is still in the 70's. It'll be set before the hot afternoon temps get there. Once the construction joint has been made you can go to a less thixothropic mix for fairing. I'd still do some undercutting and go for a fileted joint between the pipe and transom.
Capt Pat, That oval exhaust looks sweet...once again a picture is worth a thousand words...did you run the generator exhust through the pt side? BH
1966 31 Bahia Mar #316-512....8 years later..Resolute is now a reality..Builder to Boater..285 hours on the clocks..enjoying every minute..how many days till spring?
Who is online
Users browsing this forum: Bing [Bot] and 162 guests