Cockpit Panels; Replacements
Moderators: CaptPatrick, mike ohlstein, Bruce
Cockpit Panels; Replacements
I'm considereing replacing the panels inside the cockpit and would like to get opinions on the best material to use that will hold up weather and the abuse? Are there fiberglass sheets with one side gelcoated that can bought and then cut to fit and painted? Or is there another way to get a durable panel? Seems like a good winter project so looking for your suggestions. Thanks...
-
- Senior Member
- Posts: 895
- Joined: Jan 3rd, '07, 00:28
- Location: Lindenhurst, NY
- Contact:
- CaptPatrick
- Founder/Admin
- Posts: 4161
- Joined: Jun 7th, '06, 14:25
- Location: 834 Scott Dr., LLANO, TX 78643 - 325.248.0809 bertram31@bertram31.com
The easy way to obtain a "tough as nails" surface when using Azak or other brand of PVC Foam Board is to epoxy laminate the exposed surface with heavy weight Formica, (or other brand of hard laminate).
The PVC surface needs to be prepped by a thorough sanding, using 80 grit, and wiped clean with acetone or MEK just prior to epoxy bonding the two materials together.
When ready to paint the laminate, sand with 180 grit and wipe clean with denatured alcohol. Apply 2 coats of Awlgrip 545 primer, final sand with 320 grit, wipe clean with denatured alcohol and apply the top coat of choice.
This hard lamination technique will work for just about any substrate including Coosa Board, plywood, lumber, and anything else that can be gripped by epoxy.
The PVC surface needs to be prepped by a thorough sanding, using 80 grit, and wiped clean with acetone or MEK just prior to epoxy bonding the two materials together.
When ready to paint the laminate, sand with 180 grit and wipe clean with denatured alcohol. Apply 2 coats of Awlgrip 545 primer, final sand with 320 grit, wipe clean with denatured alcohol and apply the top coat of choice.
This hard lamination technique will work for just about any substrate including Coosa Board, plywood, lumber, and anything else that can be gripped by epoxy.
-
- Senior Member
- Posts: 895
- Joined: Jan 3rd, '07, 00:28
- Location: Lindenhurst, NY
- Contact:
- CaptPatrick
- Founder/Admin
- Posts: 4161
- Joined: Jun 7th, '06, 14:25
- Location: 834 Scott Dr., LLANO, TX 78643 - 325.248.0809 bertram31@bertram31.com
- CaptPatrick
- Founder/Admin
- Posts: 4161
- Joined: Jun 7th, '06, 14:25
- Location: 834 Scott Dr., LLANO, TX 78643 - 325.248.0809 bertram31@bertram31.com
OK Wursty, ya' sittin' down?
My supplier in WPB, FL doesn't carry the Komacell band name, but he does sell the exact same kind of rigid and expanded PVC sheets. I just got off the phone with him and here's the current price:
Rigid PVC sheet 4'x8'x1/2" --- $275 each
Expanded PVC Foam Board 4'x8'x1/2" --- $96 each
For a difference of $180 you can buy a lot of hard laminate and epoxy to glue it on with.
The rigid sheet weighs almost 3 times the weight of the expanded sheet, so it's way heavy. Heavier than plywood... Because of the density and frictional heat, the rigid is hard on saw blades. However, you could probably get by with 1/4" rigid where you might need 3/8" expanded.
For panels that have doors, 1/2" is my prefered thickness because it leaves a pleasing edge thickness when exposed and better for hardware attachments.
I've worked with both rigid and expanded and they're almost equally as easy to fabricate. The rigid was the choice of the day when I fabricated 9 large plating tanks and needed the strength and weldability of the rigid.
Just about all that I've done on boats involved the expanded, quite often facing it with hard laminate.
It'd be a no brainer for me to choose between the two for side panels...
My supplier in WPB, FL doesn't carry the Komacell band name, but he does sell the exact same kind of rigid and expanded PVC sheets. I just got off the phone with him and here's the current price:
Rigid PVC sheet 4'x8'x1/2" --- $275 each
Expanded PVC Foam Board 4'x8'x1/2" --- $96 each
For a difference of $180 you can buy a lot of hard laminate and epoxy to glue it on with.
The rigid sheet weighs almost 3 times the weight of the expanded sheet, so it's way heavy. Heavier than plywood... Because of the density and frictional heat, the rigid is hard on saw blades. However, you could probably get by with 1/4" rigid where you might need 3/8" expanded.
For panels that have doors, 1/2" is my prefered thickness because it leaves a pleasing edge thickness when exposed and better for hardware attachments.
I've worked with both rigid and expanded and they're almost equally as easy to fabricate. The rigid was the choice of the day when I fabricated 9 large plating tanks and needed the strength and weldability of the rigid.
Just about all that I've done on boats involved the expanded, quite often facing it with hard laminate.
It'd be a no brainer for me to choose between the two for side panels...
-
- Senior Member
- Posts: 895
- Joined: Jan 3rd, '07, 00:28
- Location: Lindenhurst, NY
- Contact:
those prices are a bit high.
A sign supply or your local friendly sign guy might be able to help you over a lumber store.
For full a 4'10' 3/4 and a 4'x8' 1/4 it was somewhere between $300-$400
They actually gave me full 1" because they were out of the 3/4, same price.
Used the 10' along the sides, and the 8' along the stern, owner wanted some teak so there are 2 pieces running along the edge, or you can split the 1/4" into 2 pieces for the stern, or just order another 10' for the stern, but you come up like 1" short with the 8' depending on how you have the side panels mounted it could be more or less.
For me its easier on the customer to charge another $100 for the panel material and be done with it over labor and materials to laminate panels.
A sign supply or your local friendly sign guy might be able to help you over a lumber store.
For full a 4'10' 3/4 and a 4'x8' 1/4 it was somewhere between $300-$400
They actually gave me full 1" because they were out of the 3/4, same price.
Used the 10' along the sides, and the 8' along the stern, owner wanted some teak so there are 2 pieces running along the edge, or you can split the 1/4" into 2 pieces for the stern, or just order another 10' for the stern, but you come up like 1" short with the 8' depending on how you have the side panels mounted it could be more or less.
For me its easier on the customer to charge another $100 for the panel material and be done with it over labor and materials to laminate panels.
- CaptPatrick
- Founder/Admin
- Posts: 4161
- Joined: Jun 7th, '06, 14:25
- Location: 834 Scott Dr., LLANO, TX 78643 - 325.248.0809 bertram31@bertram31.com
Wow! Estimating 47 sq ft of panel space in B31 and rigid white PVC weighing in at ~0.624 per sq ft on 1" thick material, that's in the neighborhood of 380 lbs....
My plastics guy was quoting retail price, which is what most DIYer's will pay.
You're right that sometimes it's easier to just pass along a material price for an item that has less labor but a higher material cost.
To epoxy laminate a 4'x8' sheet of substrate with a full panel of hard laminate would take me about 1 1/2 hrs and use about 1 quart of epoxy, thickened with 2 pints of cabosil.
Using PVC Foam Board as my substrate the retail cost would be $96. The sheet of hard laminate from Lowes would be $50. A quart of epoxy about $25, and the cabosil maybe $1.
At $60 an hour for labor that's $90 + $172 in materials comes to $262 for the panel ready to fabricate from, or $9 per sq ft.
Again estimating 47 sq ft needed that's $423 for the base material to fabricate the finished panels.
Not much difference cost wise between the laminated panels and the rigid PVC.
The real difference that I see is in the weight. Roughly 325 lbs in rigid vs roughly 100 lbs n expanded w/ laminate. No question that a B31, especially diesel powered, won't notice the extra 225 lbs in the cockpit, but it's weight that has to offset for fore and aft trim. 60% total weight aft of the fwd engine space bulkhead is near ideal for a bow proud cruise without squatting or plowing on a B31.
My problem is that I build like was building for someone else, which is usually far better than I would build the same item for myself. At the same time, I charge the customer like I was paying the bill...
My plastics guy was quoting retail price, which is what most DIYer's will pay.
You're right that sometimes it's easier to just pass along a material price for an item that has less labor but a higher material cost.
To epoxy laminate a 4'x8' sheet of substrate with a full panel of hard laminate would take me about 1 1/2 hrs and use about 1 quart of epoxy, thickened with 2 pints of cabosil.
Using PVC Foam Board as my substrate the retail cost would be $96. The sheet of hard laminate from Lowes would be $50. A quart of epoxy about $25, and the cabosil maybe $1.
At $60 an hour for labor that's $90 + $172 in materials comes to $262 for the panel ready to fabricate from, or $9 per sq ft.
Again estimating 47 sq ft needed that's $423 for the base material to fabricate the finished panels.
Not much difference cost wise between the laminated panels and the rigid PVC.
The real difference that I see is in the weight. Roughly 325 lbs in rigid vs roughly 100 lbs n expanded w/ laminate. No question that a B31, especially diesel powered, won't notice the extra 225 lbs in the cockpit, but it's weight that has to offset for fore and aft trim. 60% total weight aft of the fwd engine space bulkhead is near ideal for a bow proud cruise without squatting or plowing on a B31.
My problem is that I build like was building for someone else, which is usually far better than I would build the same item for myself. At the same time, I charge the customer like I was paying the bill...
-
- Senior Member
- Posts: 895
- Joined: Jan 3rd, '07, 00:28
- Location: Lindenhurst, NY
- Contact:
a 4x8 sheet of 1" comes in at 124lbs, we used the 1" because that is what they had and it was a few weeks for something thinner
We used maybe 2/3 of the sheet
scrap was a 9" strip down the middle (the edge had a really nice bevel we wanted to use along the deck so we cut from each end ) and a full width scrap 22" on the end. On the dusty old bathroom scale it came in at 40lbs or so.
The weight is not all that bad.
It is just hard to justify charging a customer to make a glass panel that large, by the time gelcoat, matting, resin, labor, etc. versus picking up a sheet in the morning and being done by the afternoon. Around here $60 a hour you would be losing money so you have to pick and choose your projects when it is someone else paying the bill. We are also discussing panels that were originally thin I dont know what covered with formica and they lasted 30+ years, nothing structural.

We used maybe 2/3 of the sheet
scrap was a 9" strip down the middle (the edge had a really nice bevel we wanted to use along the deck so we cut from each end ) and a full width scrap 22" on the end. On the dusty old bathroom scale it came in at 40lbs or so.
The weight is not all that bad.
It is just hard to justify charging a customer to make a glass panel that large, by the time gelcoat, matting, resin, labor, etc. versus picking up a sheet in the morning and being done by the afternoon. Around here $60 a hour you would be losing money so you have to pick and choose your projects when it is someone else paying the bill. We are also discussing panels that were originally thin I dont know what covered with formica and they lasted 30+ years, nothing structural.

I was very happy with how the azek came out. While it may scratch, the scratch is the same color as the material so it is hardly noticable. Picked up lots of extra storage. Looks way better than what I had. Easy to work with.... got lots of good tips from this site. Attached motorcycle inner tubes to my rod holders to divert the water into the bilge so the storage is dry. Pix below..ignore the old fart in the "library". Location - montauk Pond.
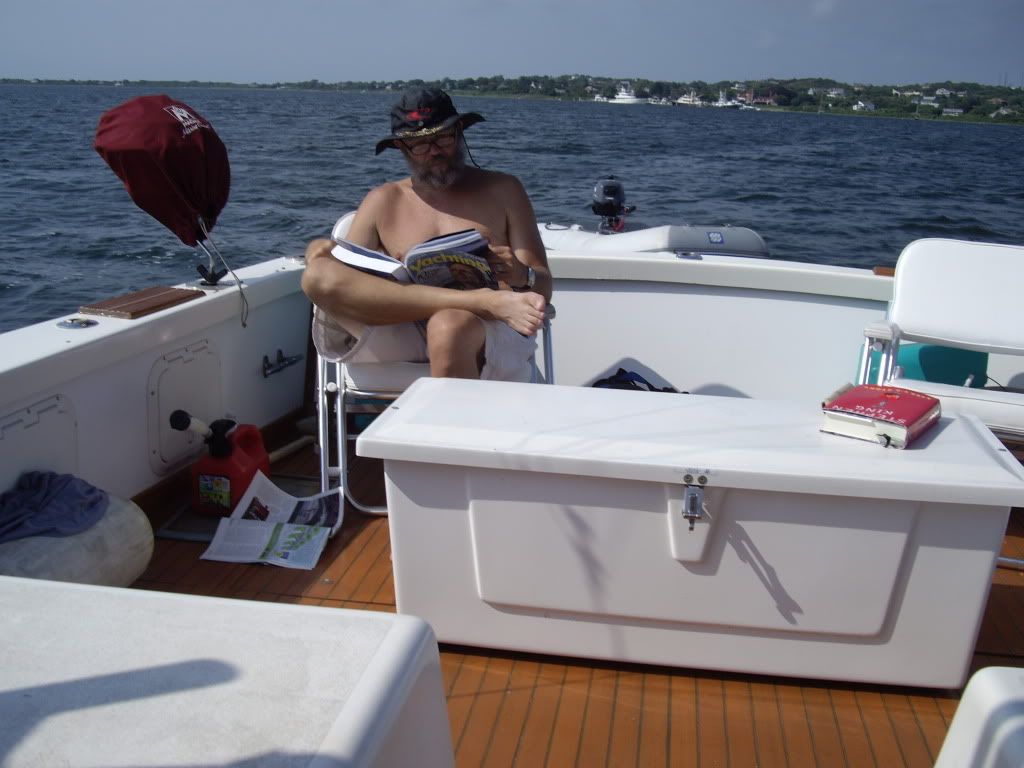
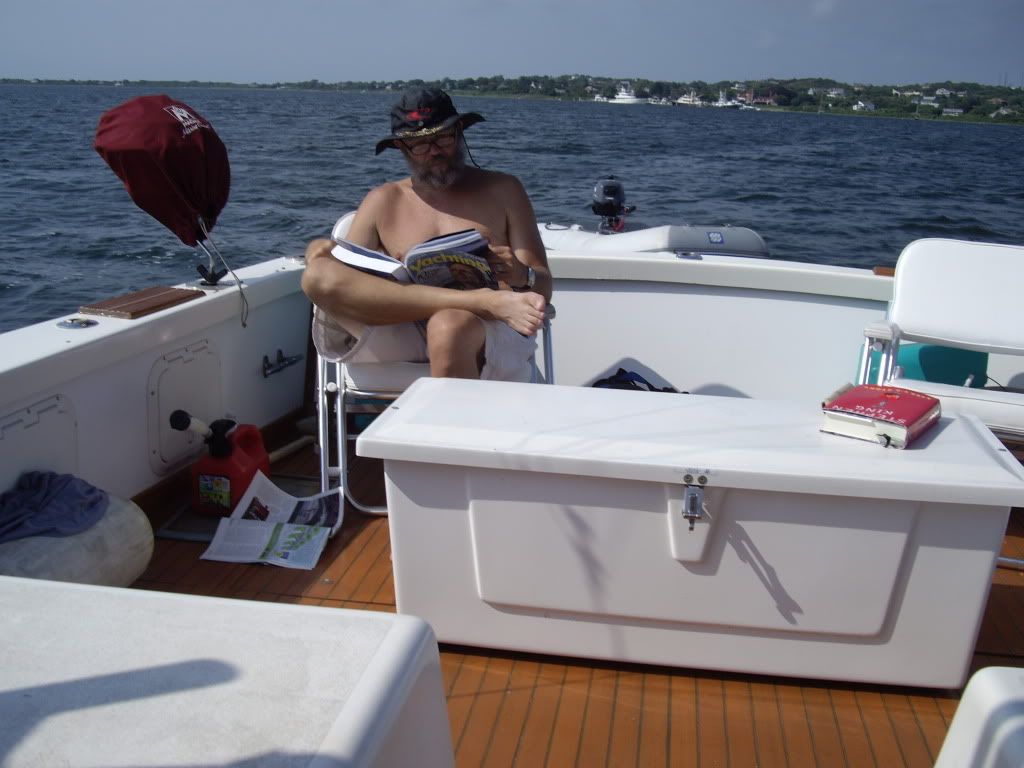
Giff
-
- Senior Member
- Posts: 6947
- Joined: Jun 29th, '06, 21:24
- Location: Hillsdale, New Jersey
- Contact:
-
- Senior Member
- Posts: 895
- Joined: Jan 3rd, '07, 00:28
- Location: Lindenhurst, NY
- Contact:
it takes alot more to scratch the komacel, definitely worth finding. It also has a slicker finish that seems like it would be much easier to keep clean
Bob- same theory being used here- install panels, use as-is, if 10 years later they are yellowed or discolored paint them then, but a little yellowing will bring them closer to the original bertram color so who knows ?
Bob- same theory being used here- install panels, use as-is, if 10 years later they are yellowed or discolored paint them then, but a little yellowing will bring them closer to the original bertram color so who knows ?
-
- Senior Member
- Posts: 895
- Joined: Jan 3rd, '07, 00:28
- Location: Lindenhurst, NY
- Contact:
-
- Senior Member
- Posts: 6947
- Joined: Jun 29th, '06, 21:24
- Location: Hillsdale, New Jersey
- Contact:
Who is online
Users browsing this forum: Bing [Bot] and 481 guests