I am ready to put the new strut & rudder backing in. Grinding the old cabosil and epoxy out was easily the worst part of this process to date. 1.5 - 2 hours per side with a 40 grit grinding pad. My whole body hurts.
The backing that was removed was one 15" x 36" long plywood piece. I was shocked that parts of it were wet after 2 years out of the water. I was also shocked at the number of air pockets in the cabosil/epoxy that held the plywood down.
The new piece is 18-3/8" W x 40"L. Here is an image of the cut piece being test fit:
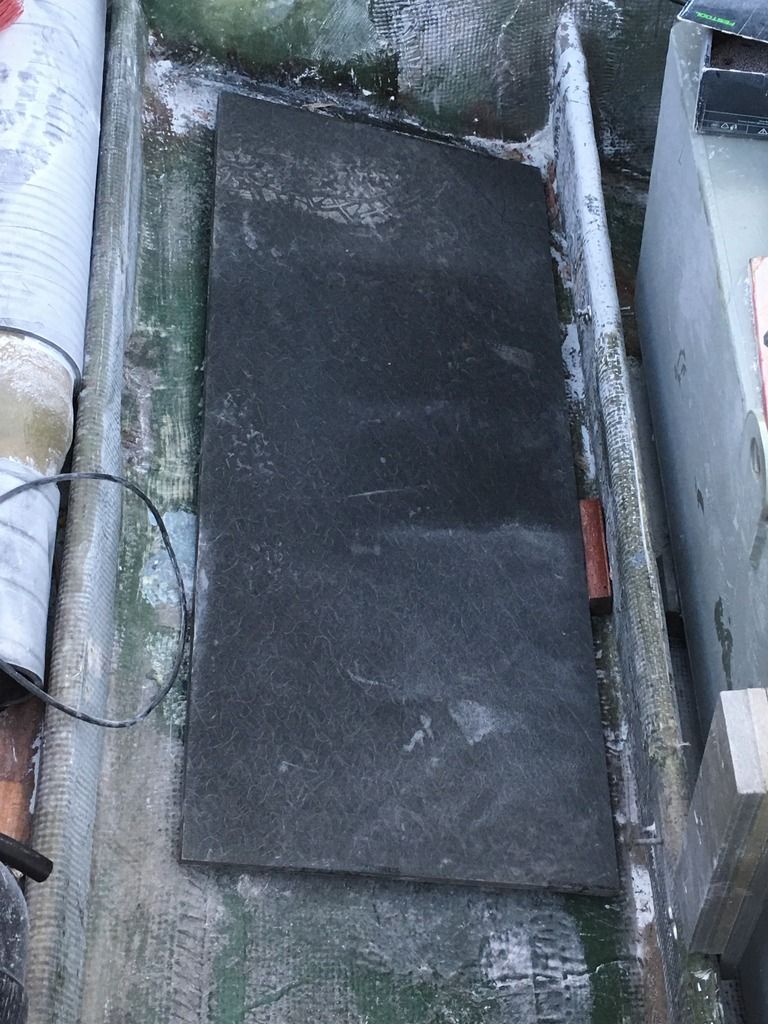
The new piece ends up 26.5% more square inches than the original (735 vs 540 square inches).
I'm following Capt Patrick's vermiculite/cabosil/epoxy recipe and instructions. The bottom of the Coosa has a layer of 1708 biaxial fiberglass already. The only question/concern I have before I put this in permanently is about which adhering dimension is more important: The square inch size of the Coosa backing that is adhered to the hull with the cabosil/vermiculite/epoxy or the square inch size of the biax and epoxy that covers the backing plate. If you look at the picture you can see there is a limited amount of space to lay up the biax on the inboard and outboard sides. Here are the options as I see them:
1. Fill the gap between the inboard stringer and backing with rounded cabosil & epoxy and take the biax up and over the top of the inboard stringer. Take the biax on the outboard side up to the stringer. Logic here is square inches of biax on top of the backing is as important to the overall rigidity and load distribution of the backing section that is adhered to the hull.
2. Trim the Coosa backing from 18-3/8" to 15" wide to allow more adhesion area for the biax that goes on the top of the backing to the hull.
3. Glass it in as it sits in the picture and not worry about the number of square inches of the biax on the top adhering to the hull on the inboard and outboard sides because the structural rigidity of the Coosa backing being adhered to the hull with cabosil/vermiculite/epoxy is where the actual strength of the load distribution lies.
All feedback on which option achieves the best load distribution in the event of a grounding is greatly appreciated.
Thanks,
JohnV8r